Projects
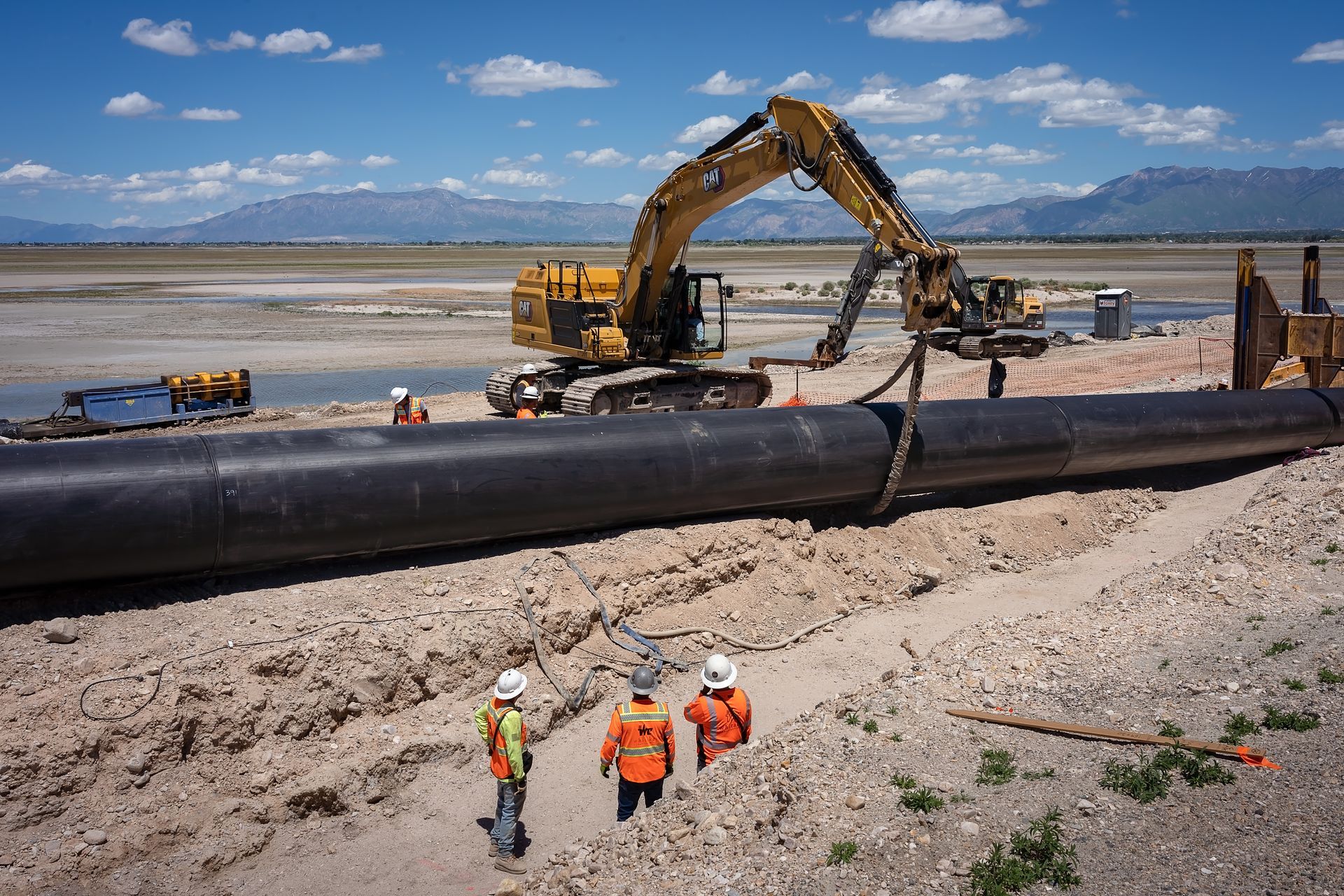
Crews from Whitaker construction installed a massive 63-inch diameter HDPE pipe for North Davis Sewer District that allows treated and cleaned wastewater to flow to the Great Salt Lake, putting water back into the ecosystem while combatting dropping water levels. (photos courtesy Whitaker Construction)
Work continues to grind forward on the mammoth new Salt Lake City Water Reclamation Facility (WRF)—a critical $850 million project being built by a joint venture of the Salt Lake regional offices of Sundt Construction and PCL Construction that will replace the current facility in North Salt Lake once it's turned over to SLC's Department of Utilities (SLCDPU) in July 2026. As it stands, this is the second-largest project in City history, trailing only the recent $2 billion-plus Salt Lake International Airport Redevelopment (Phases 3-4 ongoing), and one of the most technically challenging projects in the state. "We are up for the challenge every day—the magnitude of this thing is unreal," said Manny Diaz, Project Manager for Salt Lake-based Sundt, as he drove around the massive 30-acre site in late-January, a worksite teeming with 300 current employees (it will peak at 400 workers this summer) and myriad complicated structures being built simultaneously. Diaz is a long-time veteran of the water reclamation facility industry—this project marks plant No. 26 in his own personal history—and he was brought in a year ago by Sundt because of his expertise. When he arrived in Salt Lake at the beginning of last year, it was right smack dab in the middle of what proved to be a record-breaking year for snowfall. "It was quite a welcome to Utah!" Diaz chuckled. "We keep very close tabs on the weather." And while crews haven't been subjected to the same inclement weather this winter, site conditions are still generally wet and muddy, and the difficulties associated with building the various structures are constant. Crews are nearing the halfway mark, so certainly it's a milestone worth acknowledging, even though a mountain of construction is still left to climb. "It's such a huge accomplishment to be this far," said Jason Brown, Deputy Director of Public Utilities for SLC. "We've faced a lot of challenges, Covid, material shortages [...] it's amazing to be part of a team that works so well together. We still have a long way to go, but we'll get there. We've made a lot of progress and should be proud, but it's hard to celebrate success with so much work still ahead." Diaz, along with PCL Project Manager Shayne Waldron, said crews recently achieved a major milestone: one million hours worked, a notable accomplishment. “Achieving the ‘one million hours worked’ milestone is a testament to the coordination and collaboration required of a project this size," said Brown, adding that the new WRF project benefits from regular and ongoing staff collaboration, under the watch of Sundt/PCL, designers AECOM and Jacobs, and SLCDPU leadership. “This [milestone] is the culmination of many different efforts,” added Mauricio Ramos, District Manager for PCL’s Civil Infrastructure Division. “From local engineers to pipe layers, journeymen, construction trade workers, foremen, and general laborers, every team member has been instrumental in reaching this benchmark. The collaboration between PCL and Sundt has been a testament to our shared commitment to excellence and innovation.” "Our crews are working together seamlessly to ensure that the final product meets the goals and needs of the community," said Sam Reidy, Senior VP and District Manager for Sundt. "Celebrating this milestone recognizes the hard work and commitment each member of the project team has made to this project and the Sundt/PCL partnership." Diaz and Waldron said soil conditions challenged the team right out of the gate and took significant time to stabilize the site. "At the very beginning, the project was designed to be built on top of where the sludge beds were at, but it turns out the sludge beds were on shaky ground," said Diaz. "This whole area is young in age, so it's all soft clays and sands," added Waldron. "Soft clays are compressible, so the big issue is settling. It would have [cost] $80 million in piles to shore it up, and then in between buildings you have all the pipe and utility duct banks, so they would almost need to be built on piles." Waldron said the idea came up to pre-load the whole site, where crews built a flat pad, installed wick drains, then pre-loaded 30 ft. of dirt, with drains going down 125 feet and providing a way for water to be pushed out of the clay. "We had over seven feet of settlement," said Waldron. Crews also set up sophisticated monitoring equipment "to see where ground was settling and what layers were compressing the most. It was really scientific—a lot more than I've seen before." Diaz said it took six months to haul in the fill dirt where it remained in place for eight months, then took another six months to excavate out—close to one million yards of total material. It was an exhaustive process, with an average of 400 trucks per day and close to 500 trucks hauling 18,000 tons on the best day. Having a cohesive, highly collaborative team of designers and construction experts has been a boon to the project schedule. Once completed, Salt Lake City’s new WRF will serve over 200,000 residents as well as those who commute downtown to work or visit Utah's capital. It will replace the City’s current—and only—wastewater treatment facility, which is over 55 years old and near the end of its service life. Maintaining reliable operations at the existing facility while constructing the new WRF nearby has been critical for the project’s success. Since breaking ground in 2019, the project team has completed approximately 65% of structural concrete work as well as soil mitigation, deep foundation work, and the installation of underground utilities. In late January crews began excavating dual 63-in. diameter pipelines, along with a 78-in. effluent pipe that is being hauled one giant piece at a time from Canada, a new type of corrugated HDPE with welded joints that should provide greater durability. All in all, crews will ultimately pour 93,000 CY of concrete and install 22 million pounds of reinforcing steel, along with 89,000 LF of underground pipe ranging in diameter from 1.5-in. to 78-in. "The camaraderie among the team members allows for a very cohesive team," said Diaz. "The only way you can tell who works for who is by the color of the truck. We have a 'one project' mentality. The complexity of the job and being trusted to lead this effort [...] have been [important] for me. It's been a great job so far." Diaz, who said his first wastewater treatment plant was in North Miami Beach in the late 80s right after he graduated from college, hopes to remain in Utah once this job is completed and turned over to the client by mid-2026. “I plan on staying here and continue to work on treatment plants in Utah,” he said. “There’s a lot of work here. We have vast experience, and we have a lot of people who want to be in Utah—it’s a great place to live. Let’s do it!”
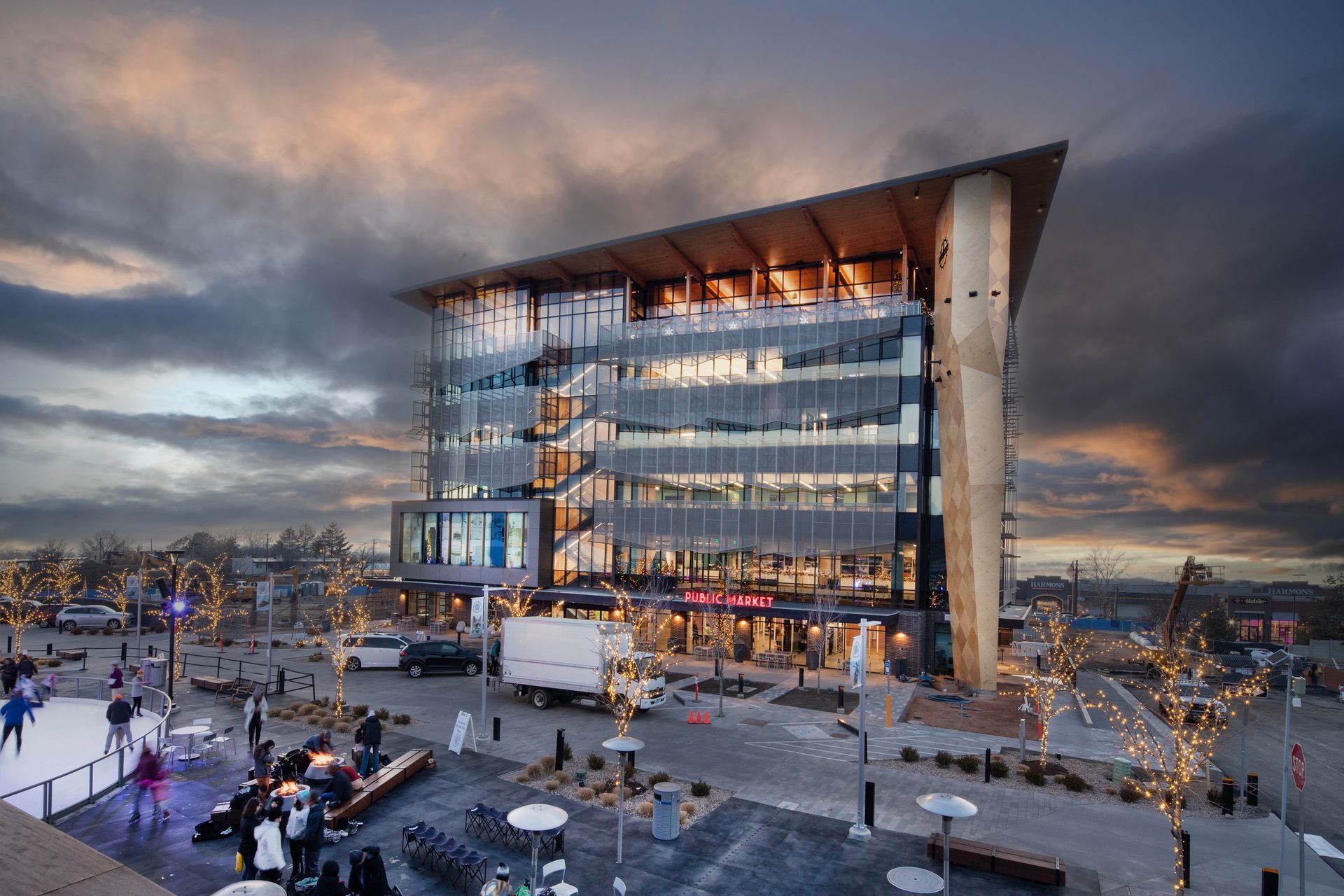
It's been a long time coming for elected officials and the citizens of Millcreek City, but their beloved $45 million, nearly 80,000 SF City Hall is finally complete, ending a lengthy five-year process that tested all parties involved but produced an awe-inspiring six-story building that will serve as the public heart of this rising community southeast of downtown Salt Lake. "It's awesome!" gushed Jeff Silvestrini, in reference to his view as he peered out across the Salt Lake Valley from his fourth-floor corner office, with captivating views via a complex glass curtain wall system highlighted with an intricate, highly functional screen shade. As the only mayor Millcreek City has known during its brief seven-year existence (it was incorporated Dec. 28, 2016), Silvestrini was recently re-elected for another four-year term (he ran unopposed) and has been a driving force behind this new project. "I could see this [view] was going to be amazing when I climbed up the crane when the concrete structure was going up. Standing on the exposed sixth floor before the curtain wall went up, I was humbled at this monumental undertaking for a new city. What we do as a city government is serve the people. We can serve the people much better in a facility like this." Unique Municipal Design Fosters Public Engagement with a "Downtown" Feel Millcreek City Hall builds upon the momentum created by the adjacent Millcreek Common to the east (opened in December 2022) to create an actual "Downtown" or "City Center" space at the bustling area of 3300 South between 1300 East and Highland Drive, which includes a host of exciting new nearby multi-family and mixed-use developments under construction. The project leverages a public-private partnership (PPP) with a local developer on an adjacent shared parking garage, along with the much-needed residential housing. Silvestrini said City leaders "did not contemplate putting City Hall here" initially, but public feedback made it clear residents wanted a downtown area to call their own. Millcreek Common—replete with an ice ribbon, splash pad, and room for food trucks—was planned as a public plaza space and has been wildly popular since its completion in late 2022. Residents also wanted City Hall to have real spaces for the public, not just a strictly-government facility, which provided exciting design opportunities for Salt Lake-based MHTN Architects, which initially worked with City officials in 2017-18 on a City Center Master Plan, which came about via a grant through the Wasatch Front Regional Council, according to Ryan Wallace, Principal-in-Charge for MHTN. "It's located roughly in the geographic center of the community and easily accessed by vehicle, transit, and active transportation—it's something that can unite the community," said Wallace. "The client has created four projects in one," aided by a vertical building mixed-use approach on the narrow footprint, a key to allowing optimum future adjacent development. "We realized early on that there was an opportunity to build a true civic center," added Silvestrini. "The more we thought about it, the more it made sense." The commitment to having a true community building is evident on the first floor, which includes a coffee house, a restaurant, and a flex public market with rotating businesses. "[City leaders] wanted an activating ground floor use that would support their idea of a downtown," said Wallace. "They didn't want City Hall to only be active 8-to-5 and then a dead zone at night." City officials and MHTN staff also drew inspiration on a tour of the new City Hall in Lenexa, Kansas, which includes adjacent common space and a ground floor retail/public market. "Everyone seemed to be thinking on the same wavelength," said Peggy McDonough, MHTN President who served as Project Executive on Millcreek City Hall. "We all felt like this was a completely unique project, unlike any other city hall that we've been a part of, and the second that has a market level. It's being looked at as an example of good development." While level 1 is sure to be a hit with Millcreek residents and visitors over time, levels 2 through 5 showcase the versatility and functionality of the project, with all essential government functions for Millcreek City, along with Unified Police and Community Emergency Response Team (CERT). Unified Police is housed on level 2 and utilizes a one-level sally port/private garage under the building (another bonus of the PPP parking garage). Millcreek City is housed on levels 3-5, with the top floor—level 6—serving as prime community space highlighted by the Grandview community room and its opulent Cross Laminated Timber (CLT) roof that evokes a natural warmth throughout the space.
Hailed as the first-ever 'Progressive Design-Build' project for the Utah Department of Transportation (UDOT), the reconstruction of US-89 project in Davis County was celebrated at a ribbon cutting June 30, marking UDOT's largest completed project since I-15 CORE in Utah County in 2012. Beyond the usual physical challenges associated with a project of this size and scope ($526 million; $384 million construction cost), this one caused significant initial heartburn among the communities impacted by the proposed right-of-way and those living adjacent to the highway, with concern over how grade separations at interchanges would compromise views. UDOT listened and made significant adjustments to satisfy public demand. "This project was for the customers, the public who lives along this corridor and those who travel through it," said Rob Wight, Region One Director. "There was some difficulty early on. UDOT gets accused a lot of times for not listening, but we do listen, and we made changes to the project that made it a better project overall. That is an asset that is going to be here for a long time." Improving public safety is always UDOT's number one goal—Zero Fatalities is forever the mantra—and the structural improvements made to US-89 spanning Main Street in Farmington to SR-193 in Layton is a major victory for all parties involved in furthering that goal. Progressive Design-Build is considered an innovative approach that combines the strengths of the design-build and CMAR project delivery methods. Its "progressive" distinction lies in its emphasis on collaboration and teamwork, uniting project owners, the design-build team, and all stakeholders. Unlike traditional design-build projects, which often limit collaboration, Progressive Design-Build (PDB) orchestrates an environment where all parties work together, steering the project's course by jointly managing risks and capitalizing on opportunities across its lifecycle. Having that collaborative cohesiveness allowed the project to wrap up in just over three years, a highly ambitious schedule that impacted a significant number of residents due to right-of-way demands. "We looked at all of the different challenges and risks associated with the project, and we thought using the progressive design-build model limited the Department's exposure [...] and gave us the ability to work through challenges in a collaborative manner," said Mike Romero, Project Director for UDOT. "It gives us more open dialogue between the contractor and owner to figure out what the critical issues are and how we can appropriately address them. You can have open, honest dialogue right from the start." "Typically, design-build projects are those that have the highest risks, and the most opportunities for innovation—not just with the owner, but the community," said Randy Jefferies, UDOT Program Director. "It's a great way to collaborate closely in an atmosphere of trust." Wight said design was at the 30% phase—around the same time the contractor got involved—when changes were implemented. "We were able to quickly revise that design [...] and make it more to what the community wanted," he said. "Progressive design-build gave us more flexibility in working with communities. We bring the contractor on in the design phase [...] and we can work through issues and risks before issuing a full contract. We took citizen input, the contractor put a price to it, and it was manifest in lowering the grade of the road. It didn't delay the project at all."

Richard (Rick) Thalman has spent the better part of the past three decades shuttling between two gigs—in the military and in the construction industry—with his current role as Command Sgt. Major for the Utah National Guard (UTNG), which gives him the chance to oversee key MILCON level projects, one of which was the restoration of the historic Officer's Club at Camp W.G. Williams in Bluffdale, completed in May by Bountiful-based City Creek Construction. The project was a true labor of love not only for Thalman, Sr. Project Manager on the $1.2 million restoration, but for many who have served in the Guard, as the iconic, nearly 90-year-old building has hosted thousands of important military events since it was originally built in 1934 and is considered the 'crown jewel' of Camp Williams. "It's a very important project for us—we wanted to do it justice and pay homage to the history, and make it more accessible to users," said Thalman, who has 32 years military service and 30 years of construction experience, including 17 years learning under the tutelage of John Cameron of Salt Lake-based Cameron Construction, himself a long-time UTNG member. "There are very few projects in my 30 years of construction that I've been able to enjoy to this level of satisfaction." Attention to Detail Critical to Project Success The Officer’s Club is on the Utah Historical Record and throughout the renovation, the Utah State Historic Preservation Office provided valuable guidance to ensure the preservation of the building's historical integrity. It's a unique, all-stone, nearly 4,700-SF building, originally designed and used as a Hostess House, providing a social hall and gathering place for mothers, wives, sisters and significant others of the men stationed at Camp Williams. It continues to be a gathering place today for special events centered around military honors, weddings, and such. When it was originally built during the great depression, it was considered a non-essential building for UTNG, but served as a “make-work” project funded largely by the U.S. government for the sake of employing local architects, craftspeople, and workmen as part of a program to relieve economic hardship in the area. "This is the second oldest building at Camp Williams and it's the most used building, so getting it renovated and doing it right with the preservation of all the historical aspects of it, that was the main goal," said Maia London, NEPA Program Manager for UTNG, checking off an extensive list of delicate, yet complex tasks. "With an historic building you find things along the way that you weren't expecting. It was the first time the building had been renovated on this scale." Restoring any historic building is always fraught with potential unknown challenges, and this project was no exception, particularly given the Guard's desire to have a full restoration of the entire building, from stone walls and wood floors to delicate ceiling tiles and windows. This scope included a myriad of meticulous tasks hand-done with old world craftsmanship, including: • Cleaning and repointing all rock masonry on the building’s interior and exterior. • Cleaning and restoring delicate hand-painted, Service Unit Crest tiles on the interior ceiling of the gathering room area. • Refinishing wood floors, including replacing some areas of the floor with new flooring that proved to be a seamless match. • Complete new mechanical and electrical systems for optimum energy efficiency, including new bathrooms and converting all original lighting to LED, including new fixtures that are excellent replicas. • A complete structural and seismic upgrade, including replacing the roof with a long-lasting wood composite shingle that replicates the original, old-style shake tiles and seismically reinforcing the roof structure. • Crafting new doors to mirror the original doors that had become damaged over time along with making the building and walkways ADA compliant. The Service Unit Crests that represent various infantry divisions and cover the ceiling in the gathering room required a yeoman-like effort, considering that some crests had become damaged over the years and required total restoration before being reinstalled. The careful cleaning of dirt, soot and smoke off the exterior and interior rock walls made it possible to see the beautiful colors in the stone and the book-end patterns that were constructed originally to create a story. Removing the dirt, smoke, and grime on 327 tons of stone which had built up over nine decades made a remarkable difference in the overall aesthetic of the building. It's easier to appreciate the perfect, puzzle-piece arrangement of the stone, and the tremendous skill and craftsmanship of the original workers. Another highlight is the craftsmanship in coving the new baseboard along the rock walls—the work was done meticulously and is a work of art in and of itself. Thalman was quick to praise Dave Swisher, City Creek Project Superintendent, and City Creek's entire team in keeping the project on track, and the many subcontractors who each completed their tasks to the highest level of quality. "There were a lot of challenges to overcome," said Thalman. "Government work isn't always the easiest [...] we have a lot of leaders so we're sometimes demanding. But they pulled it off. This is the jewel of the camp—we use it for more than just military functions, including weddings, retirements and other special events, so it really does contribute to the larger military community." "As we went along, we realized just how special it is to the Guard," said Swisher, on the importance of this job to City Creek. “The architecture is so impressive. As with any renovation there are unforeseen conditions. You have plans, but you kind of have to design and build as you go to make things right." "It's certainly one of the more difficult renovation projects we've done," said Steve Beyer, President/CEO of City Creek, who talked about the skill and patience it takes to navigate through unknown construction details as you start ripping out floors and ceilings and getting into the infrastructure of the building. "We couldn't be more proud with how it turned out. This has been a great project for us." In addition to Thalman, key UNG participants in the ribbon-cutting ceremony included: Maj. Gen. Michael Turley; Col. Vincent Wolff, G-9 director; Col. Shane Day, Utah Training Center Commander. The project also earned UTNG third place in the 2022 Army National Guard Environmental Awards.

The smokestacks that presided over Murray City are long gone and a number of new buildings have taken their place. A lot has changed in Murray City over the years. Although what's more impressive is what has been preserved for decades. You’ve seen Chief Wasatch, the giant Native American statue that presides at the mouth of Murray City Park serving as a sort of whimsical leviathan, and we've all stopped for a moment to admire the doggy in the window who is perpetually listening to the Victrola at Day Murray Music. Its apparent that Murray City has a quaint, and industrial pioneering history as well as a “Sweat of your brow” work ethic. Murray City residents and leaders want to preserve and keep telling the story by using this City Hall project as a new historical marker between what was and what will be. "We really wanted to tell the story of how Murray was formed, with the railroad being so close, the smelting, and the brick factory, it's a rich history," said David Brems, Architect and Design Principal at GSBS. The new 85,000 SF building, located at 10 East and 4800 South, uses a wide range of different materials—inside and out—to tell a mineral-rich story of how Murray City came to be such a contender in the Salt Lake Valley. Exterior brick pillars are reminiscent of the smokestacks that stood not too far away from City Hall where Murray workers operated the smelting site. The copper dias radius that makes up the council chambers is an homage to the copper smelting Murray was forged from among other Blue-Collar services. Close to the main entrance of City Hall are located Bioswales and an amphitheater that complement the sleek new exterior of the project. "Hanauer [Sreet] was actually built to be another thoroughfare to alleviate some traffic from state street and offer direct access to the front of the building," said Valarie Nagasawa, Architect and Principal-in-charge for GSBS. The running brick pattern on the exterior is iconic for the city and offers the historic aesthetic while also being energy efficient. Open areas are filled with natural light offering a well-lit corridor in any direction you choose in the building—coupled with LED lights throughout the building to lower energy consumption. There is a UV tint to the windows to reflect some of the sunlight to control heat gain on the south face of the building and blinds to mitigate glare for south-facing offices. Ballistic glass was used as part of the risk assessment as well as other portions of the building that have some bullet-resistant materials built into. The west side is for police department and has more secure points of entry. Medium Density Fiberboard (MDF) with a walnut veneer was used on many interior spaces, providing a very earth-tone feel. The importance of open space and transparency can be seen between each granite stone step leading up and down three stories of stairs. The east side of the building is open and designed for the public. You can access public planning to get your building permits and access the mayor’s office.
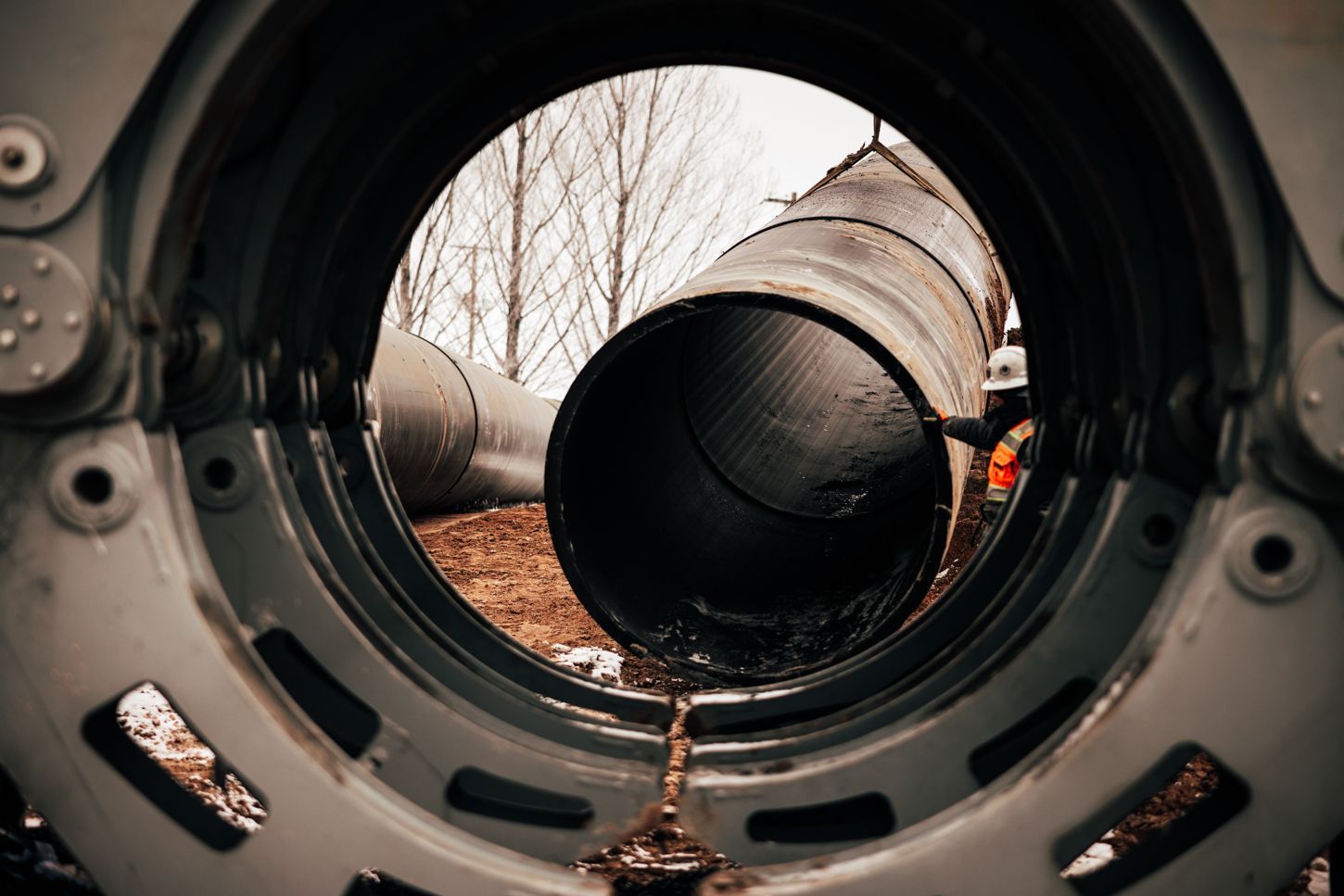
It may have required the largest HDPE pipe ever utilized in the United States with installation occurring during a record year for snowpack in Utah, but the long-term Steinaker Service Canal Enclosure Project near Vernal is now halfway complete. The canal carries water from Steinaker Reservoir to points nearly 12 miles south throughout the Ashley Valley, providing irrigation to more than 14,700 acres of land as well as municipal and industrial water users. The clay-lined canal was originally constructed in 1961-62, with initial water delivery in 1963. Recent improvement projects have been designed to turn the canal into a much more efficient pressurized pipe delivery system. According to William Merkley, General Manager at the Uintah Water Conservancy District (UWCD), which oversees the canal, the first section of the project, (Reach I), was completed in 2017 and saw the three southernmost miles of the canal converted to pipe at a cost of $10 million. The latest sections of the project, Reach II and Reach III, began in September 2022 and extend pipe nearly three more miles northward from the previous ending point, with an estimated price tag of $27 million. Irrigation was restored to water users in June. This currently leaves the canal in a hybrid condition—with half remaining an earthen canal and the other half utilizing pipeline. Due to funding constraints, Merkley said it is uncertain when UWCD will continue installing pipe on the remaining six miles. But, he noted, keeping the project moving forward is important for future water management interests throughout the Ashley Valley. “Like many areas of the state, the Ashley Valley experiences wide fluctuations in seasonal water supply and prolonged periods of severe drought,” Merkley said. “As a wholesale water supplier for both irrigation and municipal/industrial use, the Uintah Water Conservancy District feels a strong stewardship responsibility to manage its water supplies as efficiently as possible. The open canals used successfully for so many decades [need] major rehabilitation, and seepage losses common in these earthen channels are no longer acceptable.” Largest Pipe in the Nation Adapting to the current hybrid condition of the canal while updating to pressurized pipeline presents UWCD and its project designers with many unique challenges. “With each new section of canal piped, consideration of upstream conditions and structures is critical,” Merkley said. “Because higher water operating levels must be maintained upstream of the piped sections to sustain the necessary flows and head pressures, upstream farm bridges, turnouts and canal embankments all must be raised.” One of the main project challenges is what also makes it unique. Designers decided to use 78-inch diameter HDPE (high-density polyethylene) pipe—the largest diameter ever used in the U.S. Known for its flexibility and impermeability, HDPE pipe is often used to replace aging concrete or steel pipelines. “Although HDPE pipe is commonly used for canal enclosures in our region, the use of such large pipe was unprecedented,” Merkley said. “The large diameter was necessary due to the hybrid nature of our system, the shallowness of the canal’s slope, and the flows required to meet customer demands. According to Mike Cottle, Project Director for BHI in Vernal, which handled construction for the project, the large pipe diameter enables enhanced control over the water flow, minimizing loss and maximizing the efficiency of water distribution. Taking those colossal sections of 78-inch diameter pipe—each one checking in at 53 feet in length, tipping the scales at 16,500 pounds and filling an entire semi-truck load—from the drawing board to the ground itself, however, presented myriad obstacles. “Being the first to install the largest solid wall HDPE pipe in the United States, we faced considerable challenges and a significant learning curve,” Cottle said. “An early obstacle we encountered was determining how to install bends in the project. Given the pipe’s massive 78-inch diameter, we had to figure out the maximum bend radius that the Talon fusion machine could straddle over the pipe without causing damage. Once we determined this, we collaborated with the engineering team to design all the necessary bends and radiuses.” The installation of such a large pipe, Cottle said, demanded equally substantial equipment, including multiple fusion machines, 400 class excavators, articulating haul trucks and other equipment, each weighing 100,000+ pounds. “From an engineering perspective, the design incorporates innovative features to optimize the canal’s performance,” he said, adding the design also encompasses air valves, manways, drains, screening structures, and other vital components that ensure smooth operation and maintenance of the canal system.
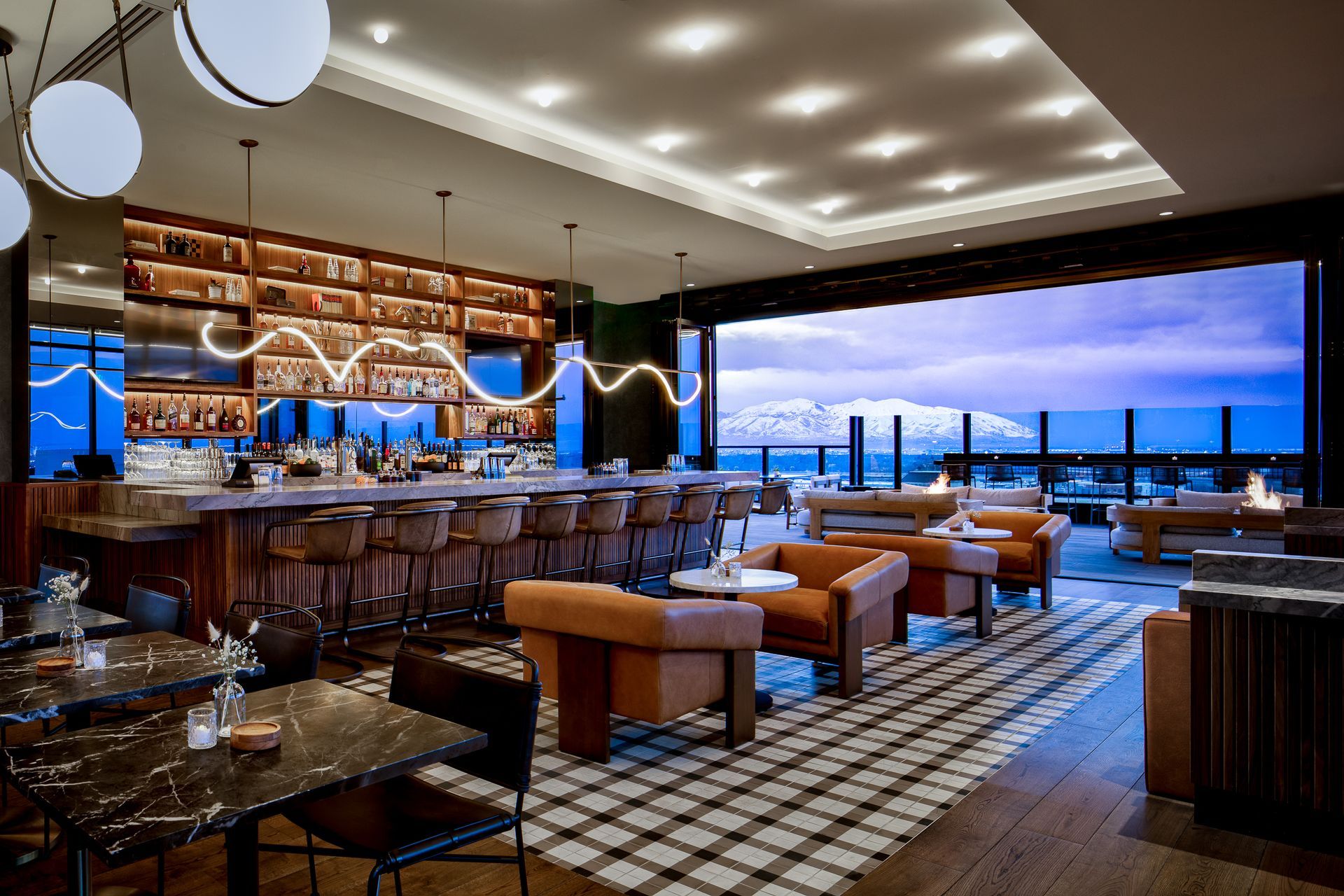
After a lengthy process spanning seven-plus years, Phase I of The West Quarter project is in the books, offering scintillating new options for downtown Salt Lake patrons in the heart of the City's west side entertainment district and transforming the 6.5-acre Block 67 parcel—kitty corner southeast to the iconic Delta Center (welcome back)—into a world-class, mixed-use development. "It sets the tone for what's to come," said Ryan Ritchie, Owner of Salt Lake-based The Ritchie Group (TRG), developer and co-owner of West Quarter along with Layton-based Garn Development. “We've had a vision for seven years—other than City Creek [Center], I think this is the most ambitious [mixed-use] project ever taken on in Salt Lake." Indeed, The West Quarter is envisioned as a revolutionary, game-changing mixed-use project that will rival similar developments around NBA arenas in other metropolitan cities, like L.A. Live, the premier sports and entertainment district surrounding Crypto.com Arena in Los Angeles, the Pearl District in Portland, and the Deer District in Milwaukee, a 30-acre neighborhood around Fiserv Forum flush with up-scale businesses, bars and restaurants. "The Ritchie Group always envisioned this project as being similar to L.A. Live or the [Deer District]," said Emir Tursic, Principal for Salt Lake-based HKS, design architect on the dual-branded hotel portion of the project. "This used to be the warehouse district, and we tried to acknowledge that in our design. That's why we have large, oversized windows, the use of brick, but we also inserted a curtain wall in the west corner, which symbolizes the transformation of this area [...] to more of a lifestyle and entertainment district. The idea is to create a district that will provide amenities to support the Delta Center and [300+ annual] events, not just Jazz games." Phase I of The West Quarter includes a pair of dynamic, 11-story high-rise buildings situated around a spacious mid-block plaza and the east-to-west Quarter Row walkway, which will gradually come to life over Phases II and III over the next five-plus years, depending on market conditions. The first building houses the first-ever Le Meridien for Marriott in Utah (and 26th in 23 U.S. cities)—a swanky, upscale hotel with inspiring interior finishes, functionality, and charm, along with the hotel magnate's 100th Element Hotel, which caters to extended-stay clients and offers its own unique style and decor. Building two is The Charles, a luxury residential tower with 240 units, offering sleek, high-end amenities—highlighted by a rooftop pool, hot tub and clubhouse, expansive workout room with an exterior component, game room areas, gourmet kitchen and more.
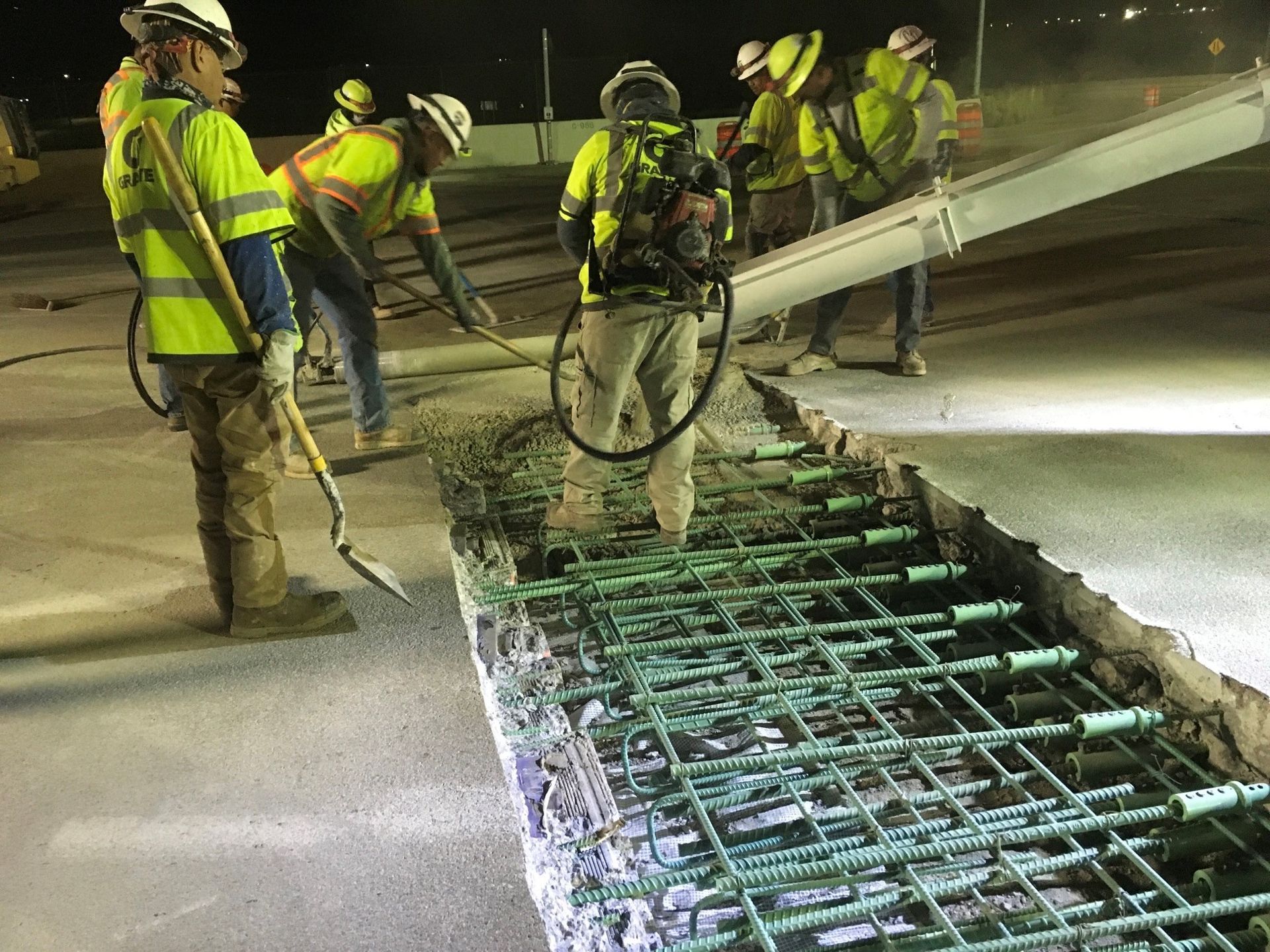
No news is good news on many a roadway project. With no hotline calls coming to the public engagement team led by Kimley-Horn, construction looked to be going off without a hitch from a public perception side, and the public was right. Like ghosts in the night, the Granite Construction team managed by Zach Schweinsberg, Project Manager, completed the SR-26 bridge joint repairs, adding new life to the confluence of roadways in Riverdale. Mind the Gap The SR-26 bridge, originally built in 2006, was working well except for two critical junctures—the expansion joints between the bridge deck and approach slab. The gap from the expansion joint only widened at the surface—nearly eight inches, according to the project team—but created ongoing issues for the traveling public. Repairs in 2013 and consistent maintenance were effective bandaids to keep the joints safe and smooth, but not permanent solutions for such essential infrastructure. At 8–10 inches wide, the bridge would need more steel, both physical and metaphorical, to endure the rigors of daily travel from an average of 52,000 vehicles. The project team wasn’t interested in chiseling away at the old to find a new solution, said Travis Jones of UDOT’s Structures Division. Instead, “We hit [the problem] with a sledgehammer.” They used the full force of expertise, high-end materials, and a best-in-class project team to close the gap for good. Fill the Gap Closing the existing joints would require a bevy of materials: rebar would nearly double in size from the previous joints, giving the joint closure the needed steel to remain closed for the life of the bridge. It led to an early complication, according to Guy Evans, Resident Engineer for designers and owner representatives HW Lochner. “We couldn’t detour people during the day,” he said. “We had to have traffic flowing in the morning” in time for everyone’s daily commute. Speed, stealth, and precision were the themes for the project, according to the various team members. Schweinsberg said the team streamlined the process by pre–saw cutting the removal phase lines in the concrete to ready it for demolition work on the succeeding night. This concrete precutting halved the projected construction time by allowing the crews to work on both joints in a single night shift. To deal with the traffic volume and limited construction window, the construction team bought in 73 CY of Rapid Setting Hydraulic Cement Concrete to work its magic. The concrete, Evans said, came in a volumetric truck that mixes the specialized concrete to exact specifications seconds before placement into the joint. “You can walk on it in an hour and drive a semi over it two hours later,” said Evans of the high-strength, quick-curing concrete. It was the perfect product to seal in steel and resiliency—and seal up the joint. Matt Rink, also from UDOT’s Structures Division, explained that each night, the project team would install traffic control, jackhammer and saw cut to remove the existing concrete and rebar, then put the new rebar back (totaling 21,821 lbs of rebar), pour the rapid-set concrete, remove traffic control, and effectively disappear—all before the clock struck 6 A.M.