Equipment dealers and manufacturers are responding to the different barriers that plague construction, but will it be enough to keep up with insatiable project demand? By Taylor Larsen
It was another record year for equipment dealers, reported Daniel Fisher of the Associated Equipment Distributors (AED). Business has been so good that the only common complaint is that dealers can’t supply for all the demand out there. Fisher, Senior Vice President for Government and External Affairs for the trade association, said that, “You go to some of our member’s [machine] yards and they have never seen them this empty.”
Parts, equipment, and machines for construction, mining, and broadband infrastructure are being snapped up at such a rate, “you are getting deposits from contractors who don’t know when it will be there and unsure how much it will cost,” he said.
With solid backlogs on available work, the current unpredictability won’t hit construction and heavy equipment as hard as it may hit other areas. There may be uncertainty with inflation, trade, and wars, but Fisher reported, “there is confidence that infrastructure construction will be able to weather the storms” of a volatile market, with infrastructure spending totaling $1 trillion over the next five to seven years.
He explained the difference between the 2008 recession and what has been happening over the last few years by detailing how the current administration’s plans for infrastructure spending $1 trillion will be done gradually, instead of on “shovel-ready” projects like what happened over a decade ago.
Demand remains powerful for equipment for ongoing and future projects but also in labor. With tons of people leaving the equipment servicing workforce from COVID, retirement, or some other reason, the need for service technicians has never been greater.
“Any one of our members would hire 10 technicians if they could,” he said. Wage increases are happening across the board, along with bonuses and other financial incentives to not just technicians, but everyone involved in equipment enterprises.
“It’s a workforce shortage issue,” explained Fisher of the dearth of equipment technicians, operators, and others that go to keep the equipment world—and job sites—operating at full capacity. “We’re all robbing each other of the same people [from other industries].”
While the supply of labor looks to catch up with demand, Fisher reported that mining and aggregates sectors are also growing to help meet that infrastructure demand domestic and international. Construction equipment demand, he said, remains hot on the news of the infrastructure package. The only struggle in equipment is in mining and exploration of oil and gas, something Fisher attributed to the current administration’s focus on emission-free vehicles and curtailing the need for fossil fuels.
But, as prices at the pump show, some adjustment on policy is needed to help America’s car- and gasoline-centric society. Advancements in electrification seen in passenger vehicles may be exciting for some, but it is not moving the needle much in equipment.
As a result, “manufacturers are moving toward more efficient equipment,” he said. Whether or not that comes from electrification will be up to consumer demand. Getting more done with less energy, he said, is always the goal, “but the diesel engine is here to stay for the foreseeable future.”
Much like other sectors of A/E/C, heavy equipment is in a good position. Will it be able to weather the ongoing labor crisis? With the three pieces of equipment that follow, the answer is yes.
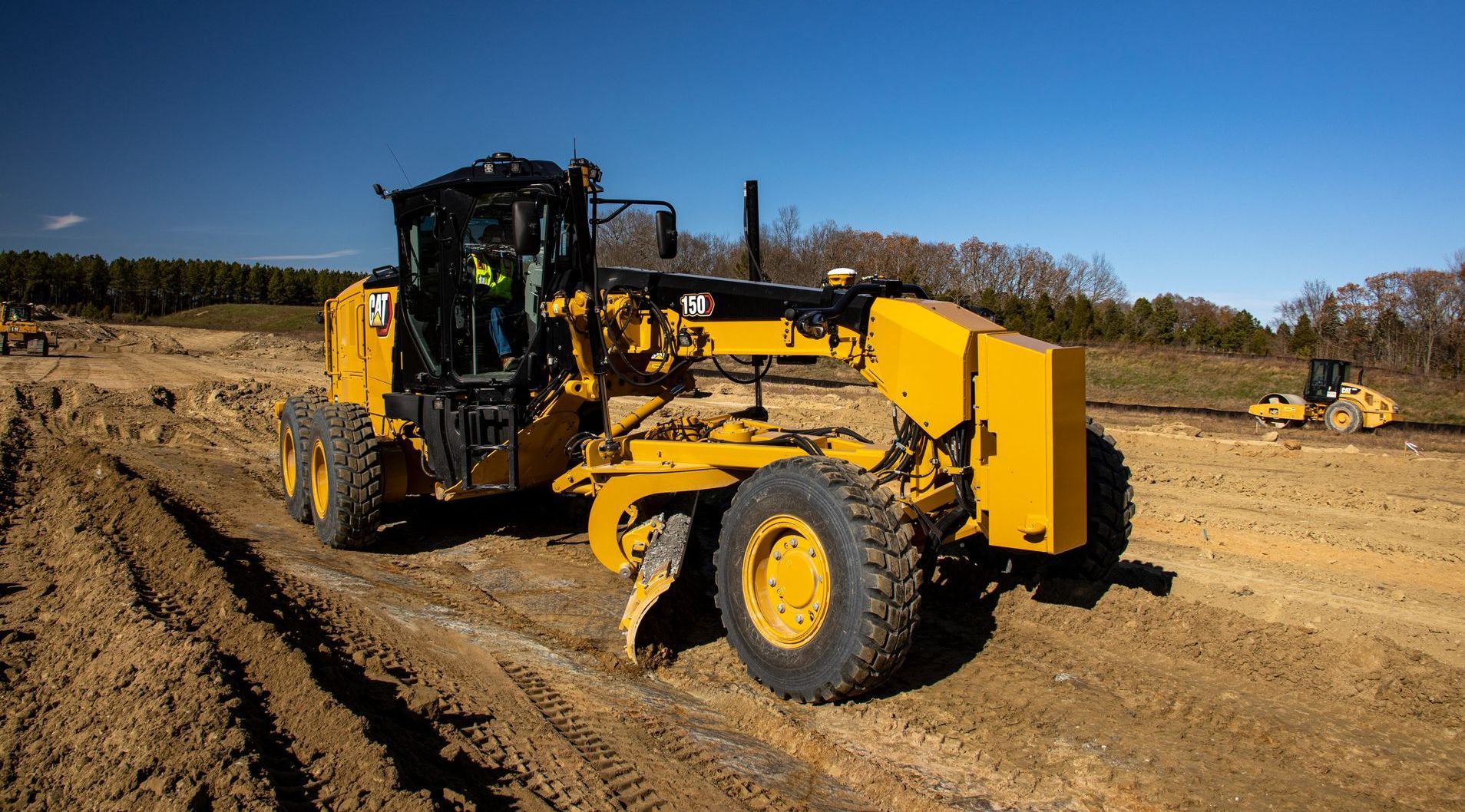
CAT 150 Motor Grader
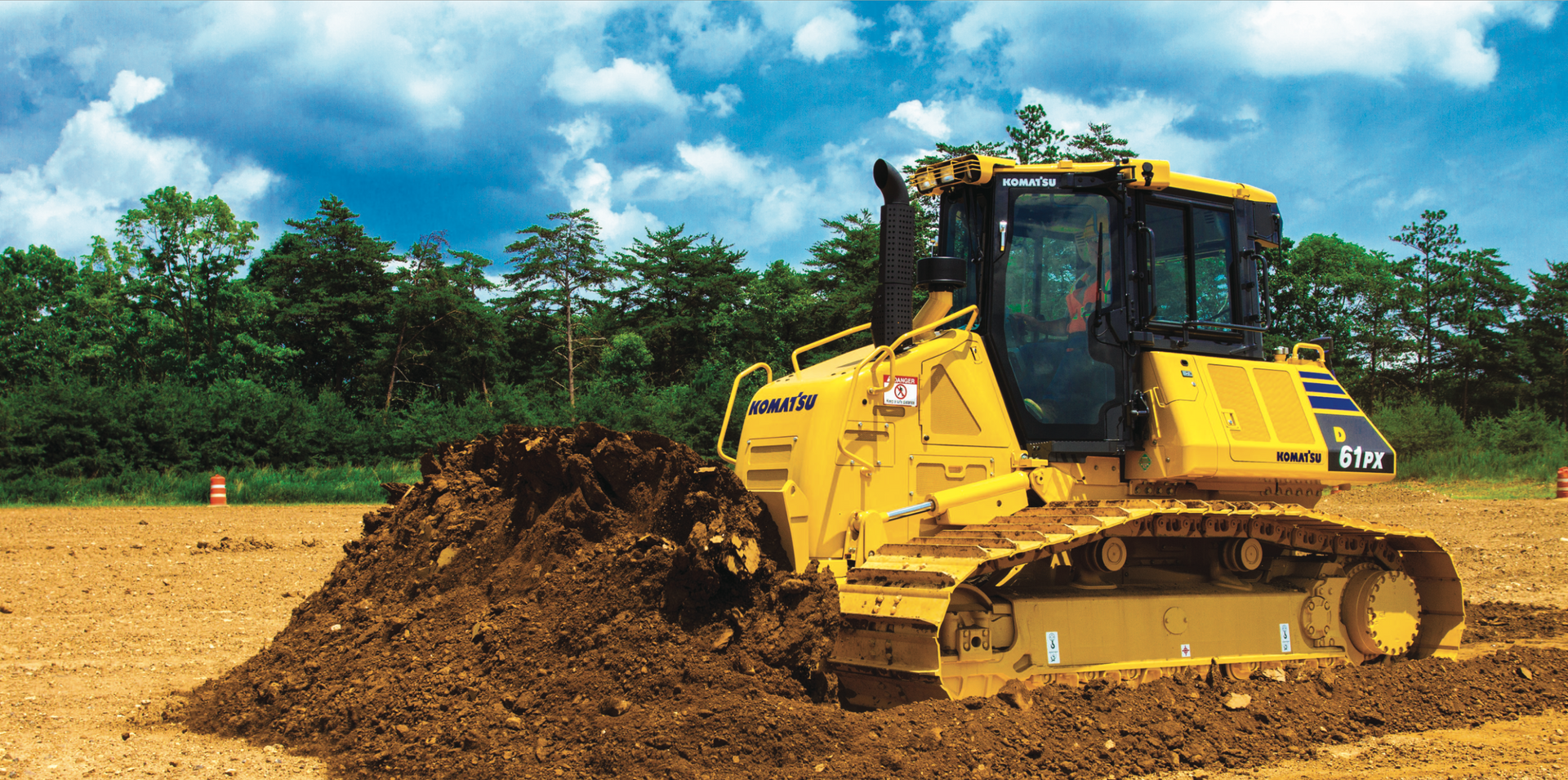
Kamatsu D-61
Make / Model: Komatsu D-61
Utah Dealer: Komatsu Salt Lake City
Komatsu’s 168-horsepower D61 line of mid-size dozers is a step in the right direction to help construction embrace not just 21st century technology, but the 21st century labor market.
“It has great visibility and is designed well from the ground up,” said Scott Despain, SMART Construction Consultant for Komatsu’s Utah office. The visibility component comes from an innovative, super-slant nose design that makes for improved machine control and increased efficiency and productivity. The physical components of the machine are impressive, but the brains of the machine are bringing huge technological efficiencies to projects to push through barriers of construction.
Some of those efficiencies are gained by the equipments’s proactive dozing features, Despain recounted. Since the machine can anticipate what is coming up for it in relation to an overall grading project, These upgraded models, via their GPS systems, “the machine is recording the existing terrain and compares it with what it needs to cut. “It’ll know whether or not it has gone over spots on the job site and make the correct passes.”
“In the old days, operator had to work their way down the grade,” said Chad Metzger, Eastern Utah Territory Manager for Komatsu. But new machines are different. It knows the scope of work, but beyond that, Metzger said that the new D-61 machines know how fast the machine is going in relation to the blade. Now, D-61 machines can run the blade at whatever rate the machine is capable of handling and push away the excess dirt to keep grade work and dozing going at full speed. Improving at the margins and making each pass worthwhile is a huge efficiency gain for today’s lightning fast projects.
It’s not just digital modeling that helps these machines, integrated systems like job site management and telematics are bringing efficiencies to so many areas of a project. Each of them said that work done in job site design and integration helps is helping to minimize the effects of the labor shortage.
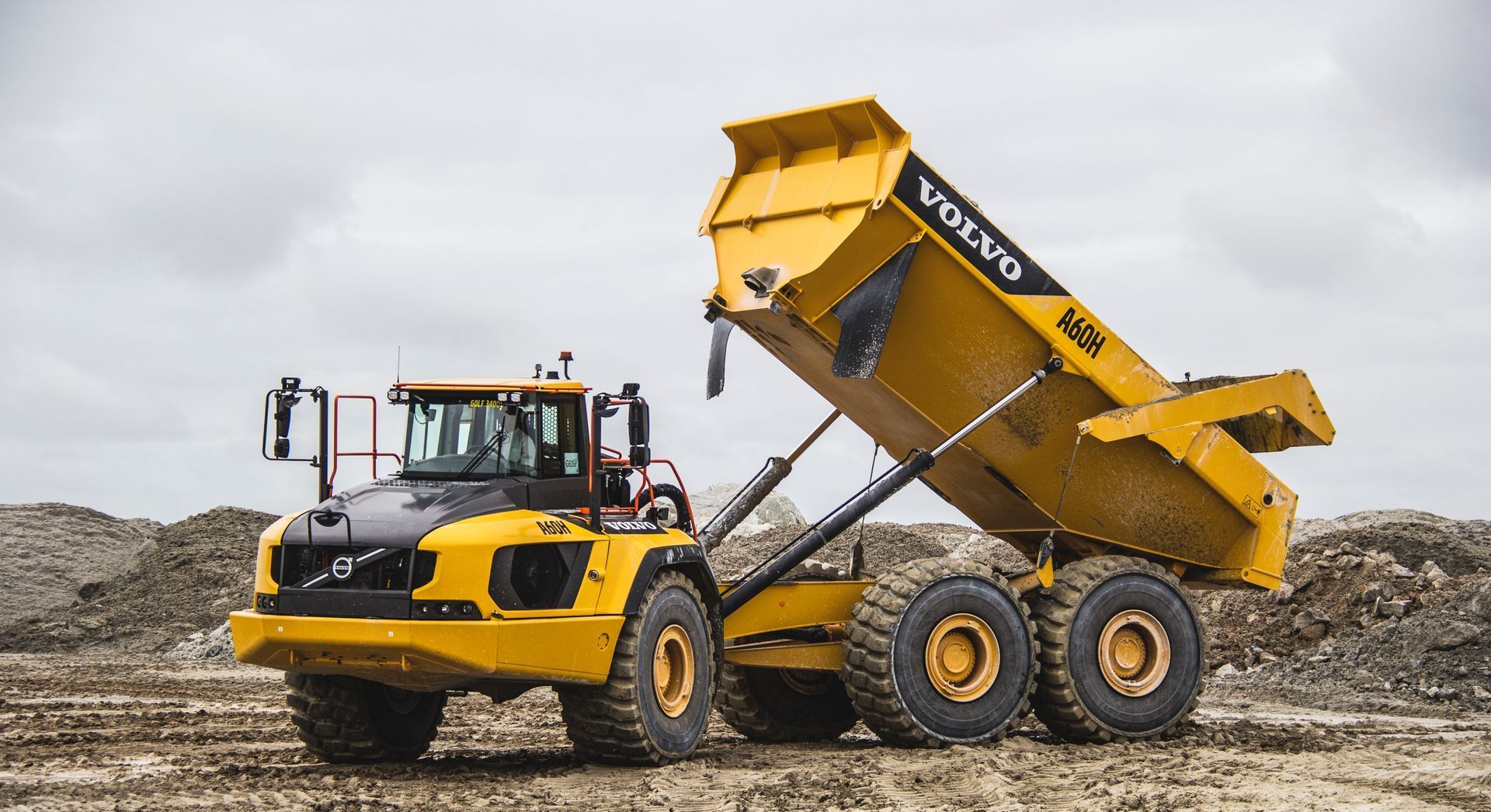
Volvo A60H
Make / Model: Volvo A60H
Utah Dealer: Arnold Machinery
Volvo is known for much more than the boxy station wagons and an unparalleled safety culture. The vehicle manufacturer’s work in heavy equipment has been a staple of the industry since the first modern articulated hauler, the 1966 Volvo DR 631, also known as “Gravel Charlie.”
Things have come a long way from that 10-ton hauler. The Swedish company’s construction arm, Volvo Construction Equipment (Volvo CE) has been hard at work advancing the articulated truck market with their most recent release of the A60H. Today, Volvo CE partners with equipment dealer Arnold Machinery in Utah and across the Mountain West on the largest operating fleet of A60H articulated haul trucks in North America monitored closely with ActiveCare.
According to statements from Arnold Machinery, the 60-ton capacity A60H is built for heavy hauling in severe off-road operations, including quarries, open pit mines, and large earthmoving operations. Where is it best served? According to the Arnold Machinery team via statement, “[The A60H] offers an alternative to rigid dump trucks and construction trucks operating on soft, uneven or steep roads, where it can haul a similar amount of material in a shorter cycle time.”
“As prices at the pump continue to soar, electric machines are becoming more and more of the conversation where the world is heading,” said the Arnold Machinery team in their statement. Manufacturers like Volvo CE are looking for electric solutions to mitigate many ongoing issues like gas prices, working in sensitive environments, and the ongoing move to curb vehicle emissions.
“You get high performance delivered with less noise, fewer vibrations and no exhaust fumes,” said Arnold Machinery in their statement. While the A60H is yet to have full electric capabilities, Volvo CE and Arnold Machinery currently offer five electric construction machines—one of the broadest ranges in the industry. With Volvo CE’s Electric Machine Management Application, construction crews can easily check battery levels, see charging status, and get notifications.
Widespread use of battery powered heavy equipment may be years down the line, but Arnold Machinery and Volvo CE are looking to stay ahead of the curve when it comes to meeting demand for electric solutions in heavy machinery.
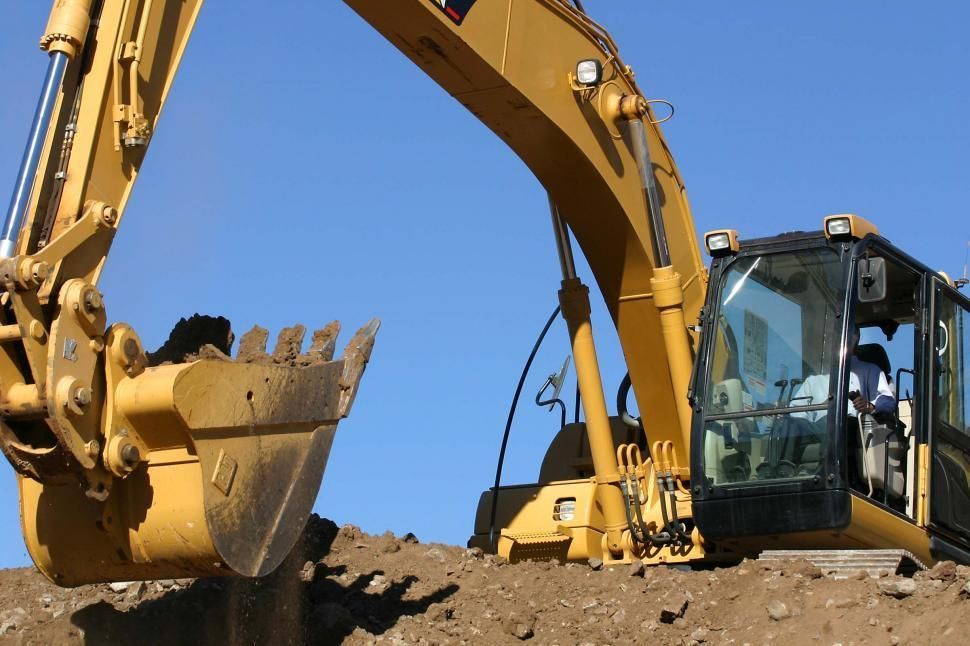
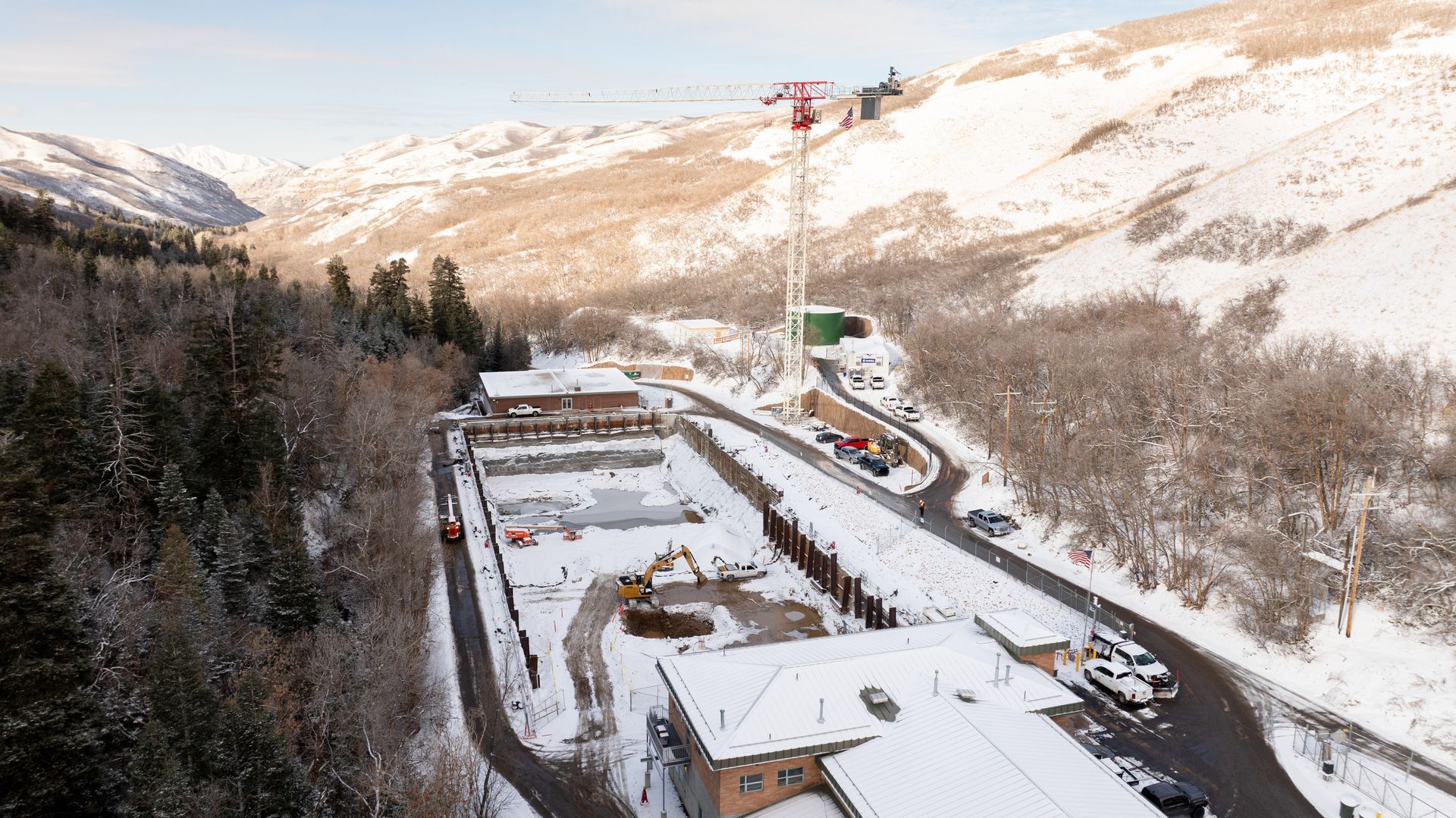
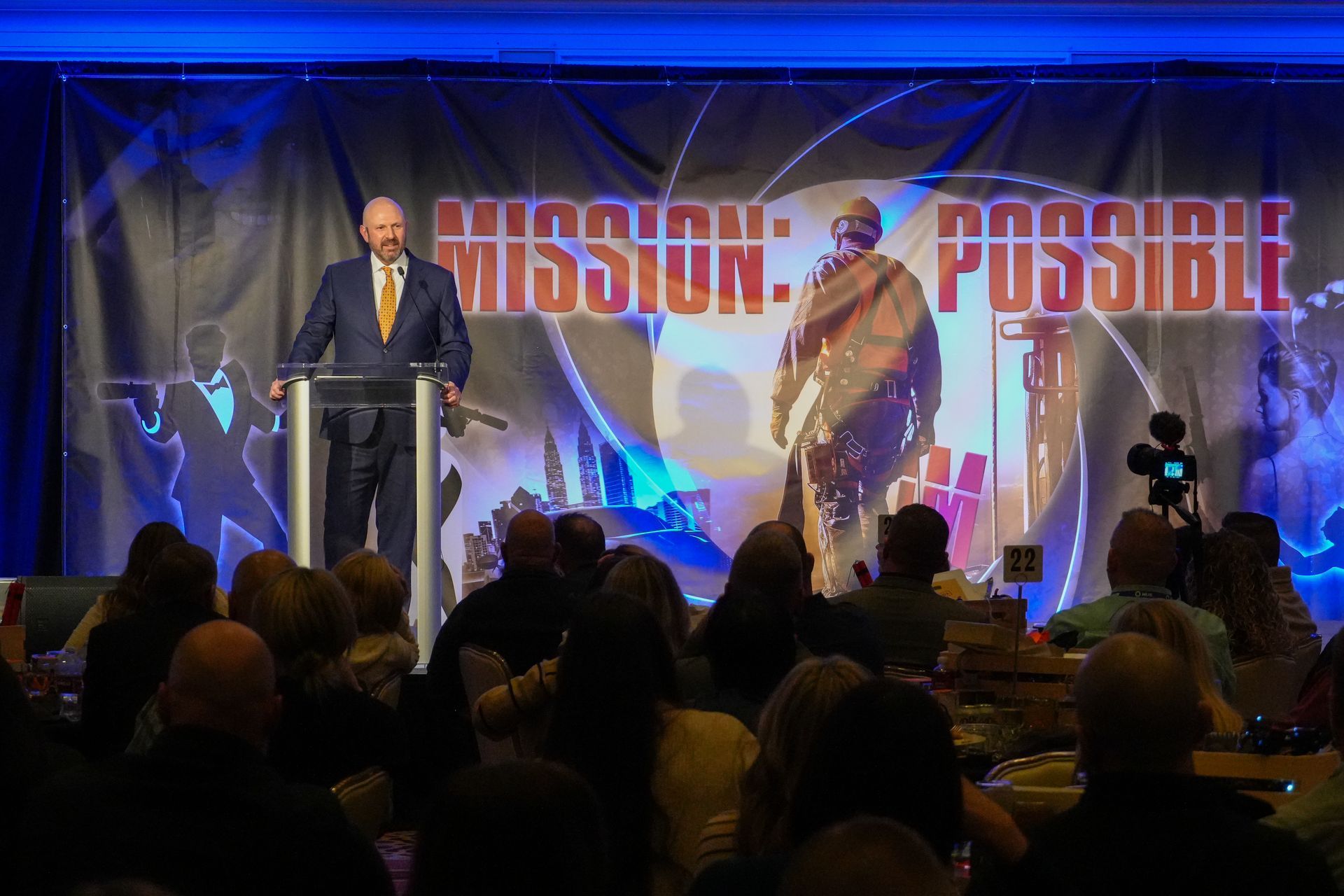
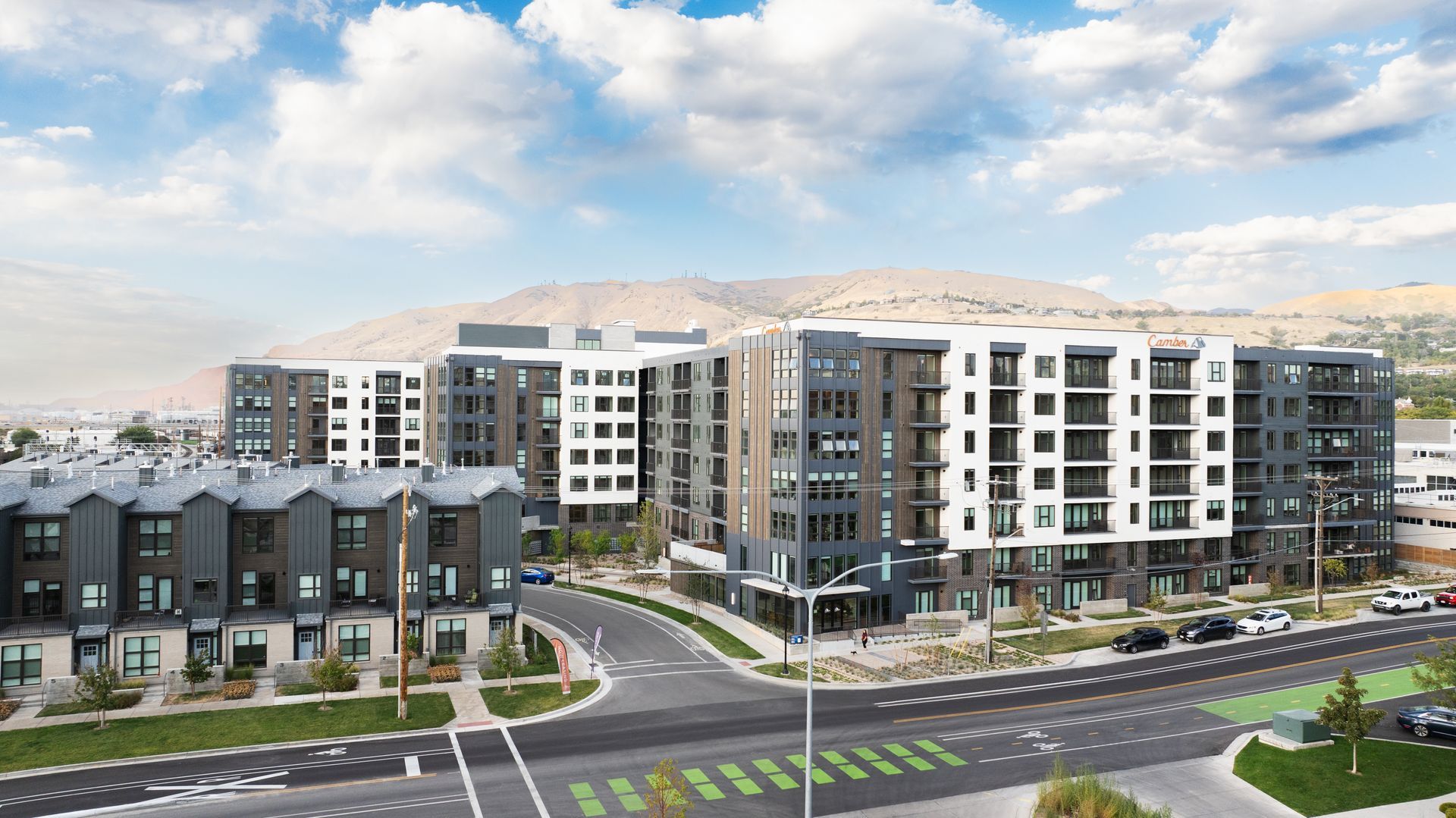
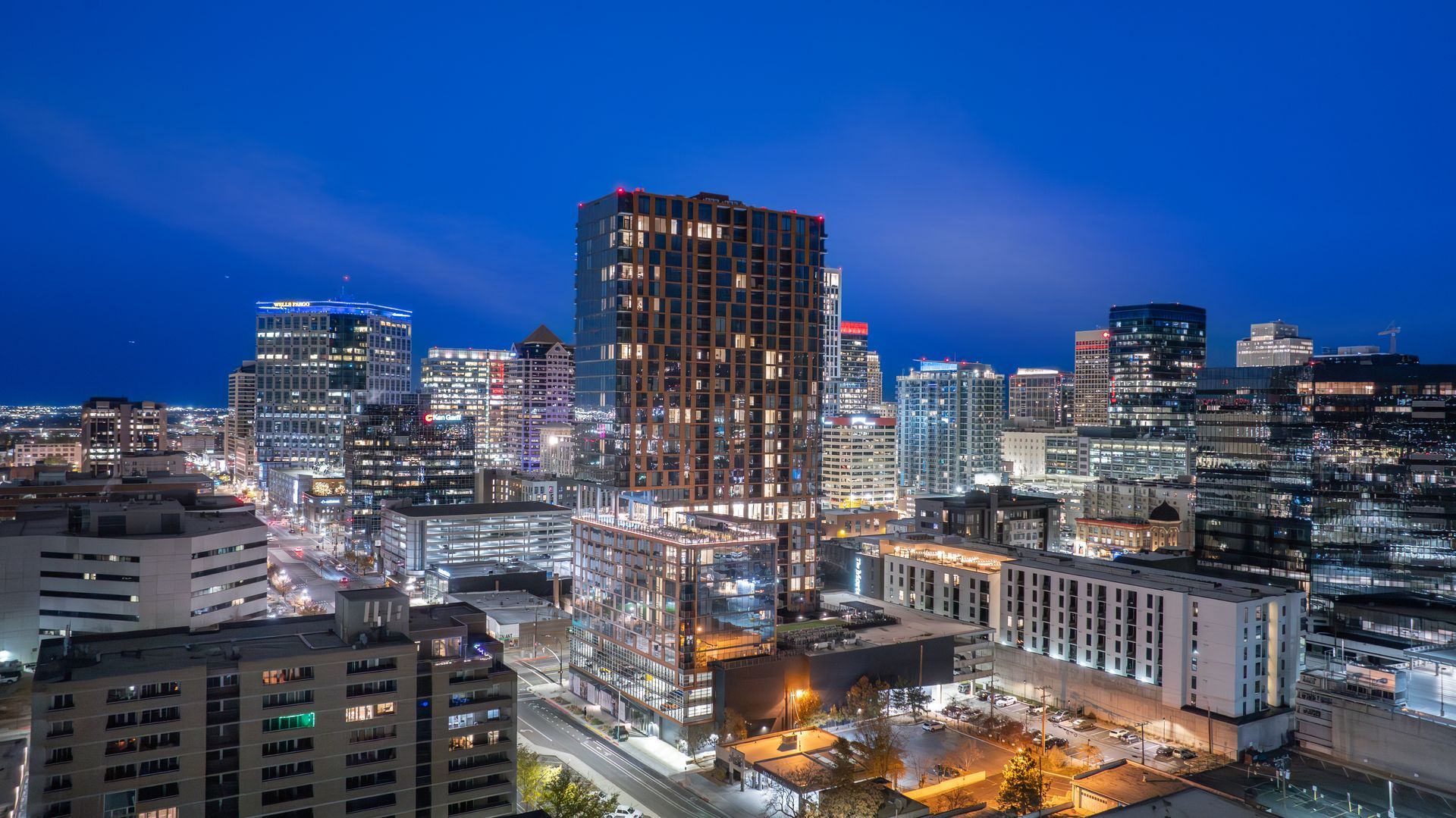
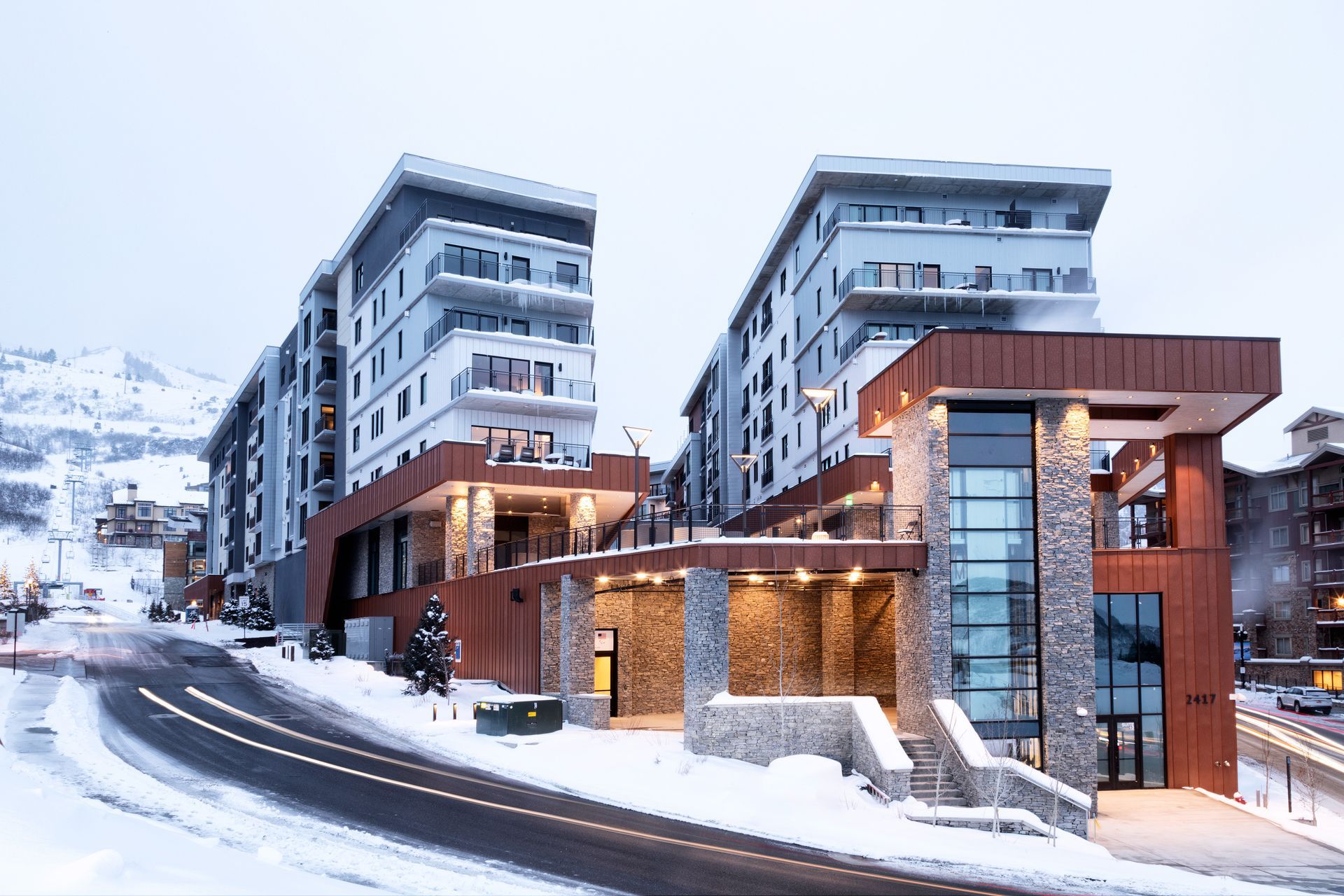
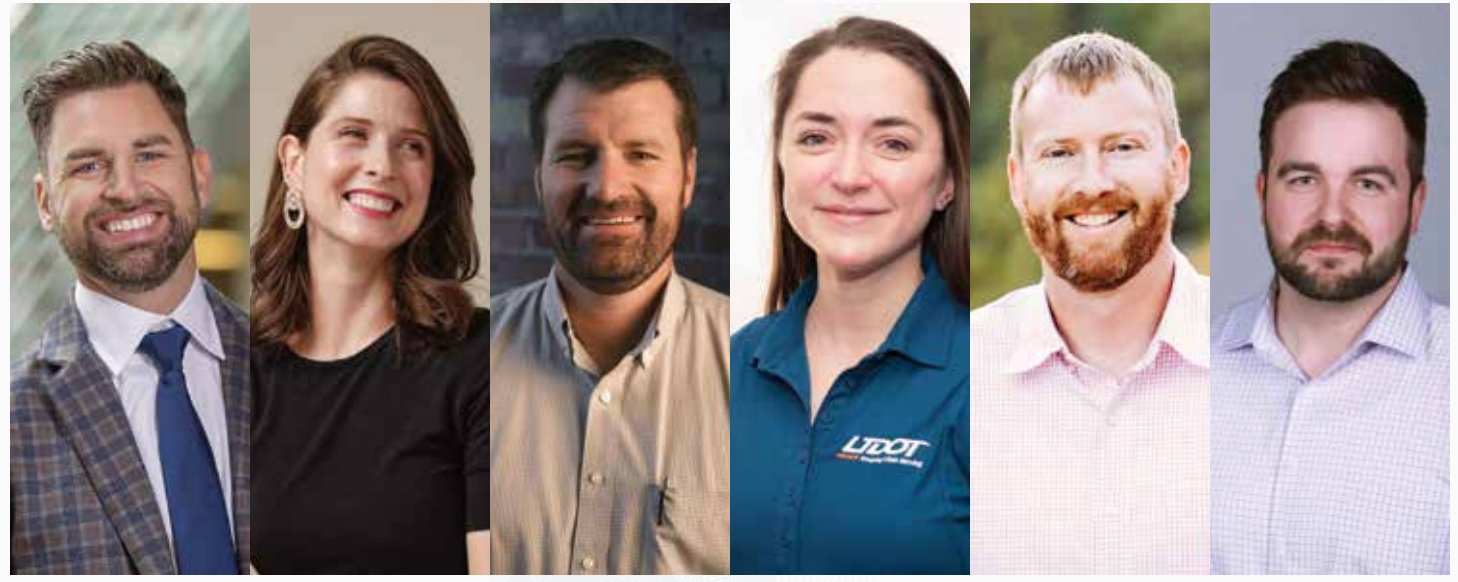
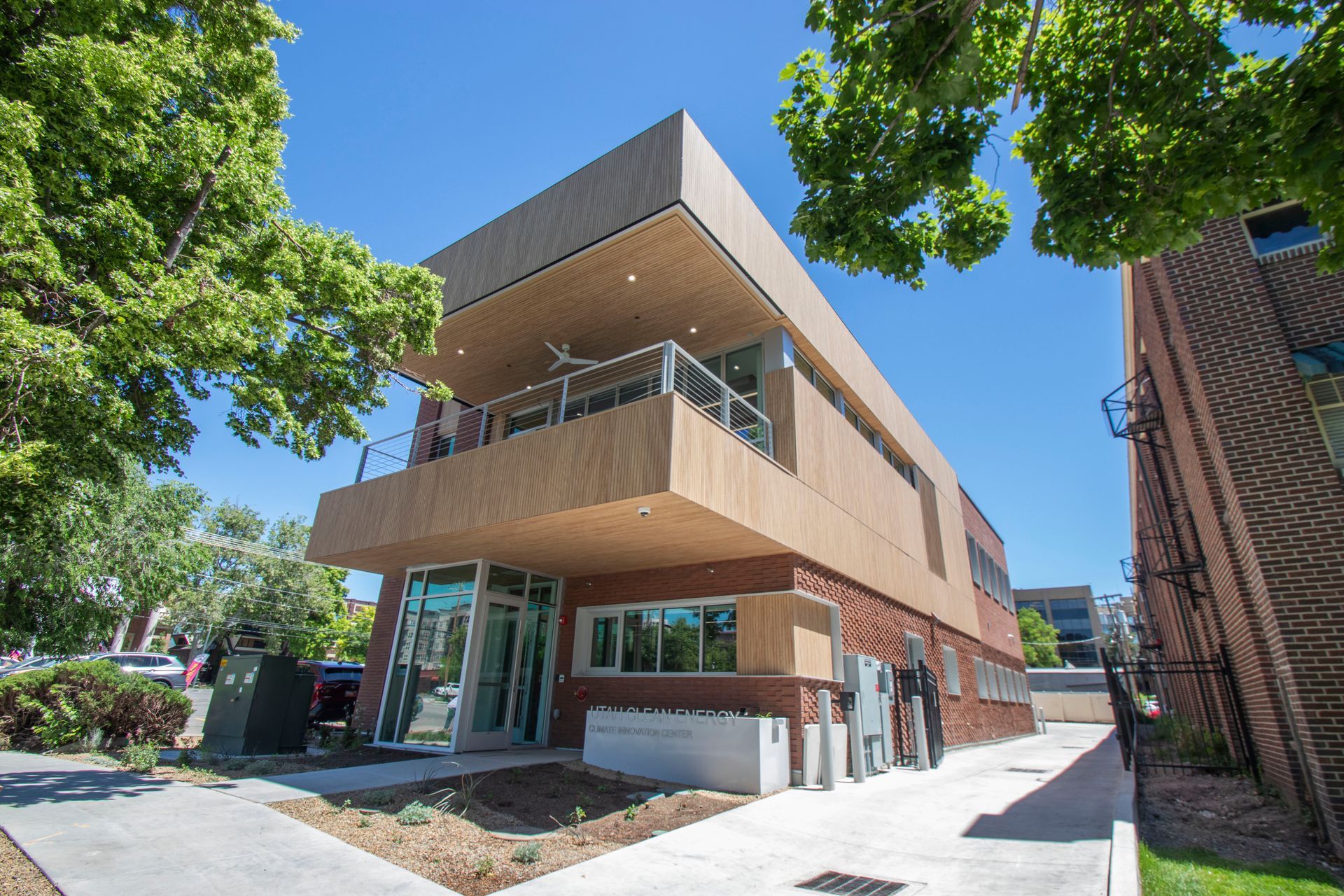