The success of the remarkable 25-story 95 State at City Creek high-rise is a testament to the dynamic collaborative effort of the entire project team. By Brad Fullmer
Already a highly ambitious and supremely technical project from a construction standpoint, Salt Lake City’s latest office tower—the ultra-sexy, 25-story 95 State at City Creek—became even more challenging when the Covid-19 pandemic struck in March 2020, forcing executives from Salt Lake-based general contractor Okland Construction to institute strict protocols to ensure worker safety.
And it was no small feat, with peak worker capacity hovering near 600 at one point. According to Zach Lewis, Project Director for Okland, every subcontractor on the job answered the bell, resulting in the project nary missing a beat and remaining firmly on schedule. Lewis expressed profound gratitude at how everyone rallied together and the collective “beehive” mentality that existed during a demanding time.
“We were in the height of building this project when Covid hit—every day I was amazed and proud and humbled by people who showed up and did their job,” said Lewis. “We were serious about mask-wearing. We got to a point where we could walk through, and everyone was wearing a mask. I take my hat off to the men and women who showed up every day and made it possible.”
Mike Jueschke, Okland’s Sr. Project Manager, echoed Lewis’ sentiments.
“I was amazed not only by workers showing up but hanging heavy steel with a mask on—not an easy task,” he said. “For a good portion of [hanging steel], we didn’t have elevators. Hiking stairs in a mask, glasses fogging up […] it was a frustration for the workforce, but they complied. We had people thanking us that we were enforcing it so rigidly so they could keep working.”
Jueschke said when it came to pouring concrete, “You can’t ‘social distance,’ so we reduced the workforce as much as possible […] and re-sequenced the direction we placed concrete to not jam people into corners.”
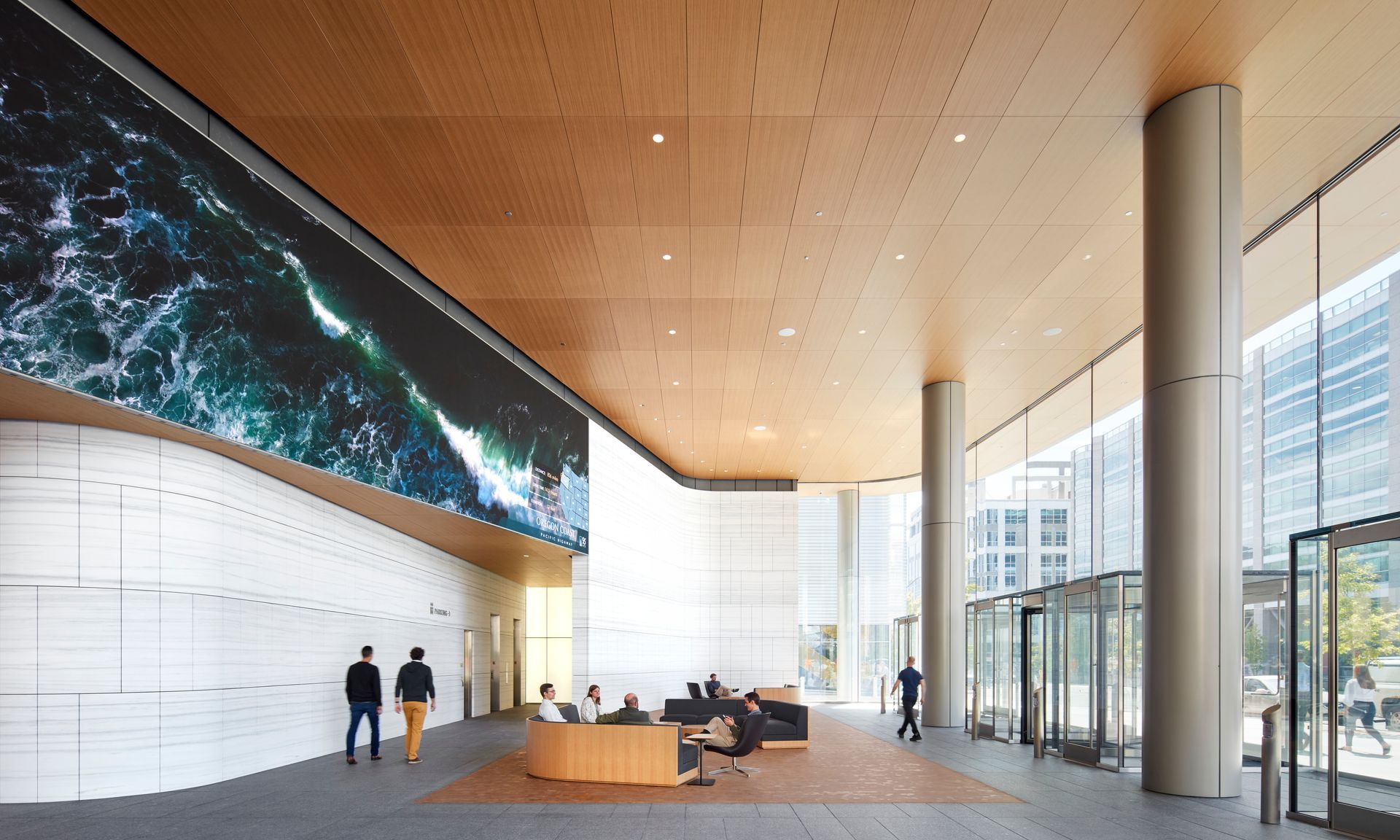
A Project Like No Other
There are many one-of-a-kind superlatives on owner City Creek Reserve Inc.’s (CCRI) second major office tower that graces Utah’s capital city—24-story 111 Main was completed in 2016—including a dynamic, highly complex structural system, the visually stunning and highly functional all-glass curtain wall system, the exquisite white Italian marble in the main lobby, and the fact that the building includes two chapels that serve a dozen wards (congregations) for the Church of Jesus Christ of Latter-day Saints.
There are many one-of-a-kind superlatives to describe owner City Creek Reserve Inc.’s (CCRI) second major office tower—the 24-story 111 Main was completed in 2016—that graces Utah’s capital city. Start with 95 State's dynamic, highly complex structural system, the visually stunning and highly functional all-glass curtain wall system, the exquisite white Italian marble in the main lobby, and the fact that the building includes two chapels that serve a dozen local congregations for the Church of Jesus Christ of Latter-day Saints, to name a few.
Designed by San Francisco-based Skidmore, Owings & Merrill (SOM)—the same architect as 111 Main—95 State at City Creek is the second phase of a multi-phase development that ties into the adjacent Harmons grocery store and parking garage that came online in 2011. A single-level basement houses mechanical equipment and parking, with the two chapels occupying the second through fourth floors. A posh fitness center and three spacious conference rooms comprise the fifth floor, which opens onto an adjacent roof garden terrace.
Beyond commercial office space and the chapels, the project includes the Social Hall Pavilion and an underground tunnel that links the tower directly to City Creek Center mall west of State Street. The pavilion is a glass-enclosed redevelopment of the former Social Hall Museum building with 1,850 SF of retail space.
SOM had up to 10 architects working on this project at one time, led by Steve Sobel, Managing Principal; Michael Duncan, Design Partner; and Sean Ragasa, Design Principal. Each said having prior experience with the client on 111 Main helped streamline the process, even though the two buildings have little in common other than their respective “wow” factor.
“We’ve done a number of projects with City Creek Reserve—the relationship goes back to work we did on the same site for the Harmons grocery store,” said Duncan, adding that SOM also did master planning on Block 75 and 76 (City Creek Mall and both sides of Main Street). “Those relationships have been positive. For a project of this scale, to have those open lines of communication and being creative together helps the success of the project.”
Jueschke echoed SOM, saying, “There was great mutual trust.”
“Our relationship with CCRI on 111 Main grew a great sense of trust between us,” added Ragasa. “It required us to be on the same page and completely aligned. We knew the same level of quality could be achieved, and that we could trust [CCRI Construction Manager] Sean Tuite to make sure this building came together the way we designed it.”
“We had to design a building as significant [as 111 Main], but different,” said Sobel. “We talked about the imagery of the building […] and how it captured the mountains behind it. It’s a different type of glazing in terms of color. The curved glass [four giant curved panels create the corners] is one aspect as the building curves on the east and west façades to capture views in a 360-degree manner—they are quite spectacular. The ‘wow’ factor is the overall composition and beautiful form that sit nicely in the city scale.” He also praised the craftsmanship and detail of the glass curtain wall system, which offers “sensational” public spaces in the lobby area.
Including two full-sized chapels make 95 State one of the most unique buildings ever designed—not only in Salt Lake but anywhere in the world. Designers were careful to make the office ecclesiastical elements different, yet symmetrical enough to look seamless in their respective aesthetics.
“The idea of contrasting commercial office space with ecclesiastical space was exciting,” said Duncan.
“We didn’t want the ecclesiastical portion to feel too rigid,” added Ragasa. “One of the things we used to distinguish the meetinghouse was the use of art glass on the north end. We came up with a cast glass pattern that varies in colors [pink and orange, blue and green], where sunlight creates great light and projects onto the street. It’s one of our favorite aspects of the building.”
Designers also prioritized sustainability, utilizing LEED and WELL Building Standard criteria to embrace sustainability from individual tenant health (WELL) to 95 State’s context in the greater built environment (LEED). The project is expected to achieve LEED Gold certification.
An ecclesiastical element—two full-size chapels and meeting rooms in the first four floors—is one of the more unique aspects of the project and serves a dozen local congregations (aerial photo courtesy Endeavour Architectural Photography). Copious amounts of natural daylighting is a staple throughout the all-glass building (photo courtesy SOM © Dave Burk)
Complex Structural System Designed
for Optimum Seismic Resistance
With the 392-foot-tall building (currently the third tallest in Salt Lake City) located within 1.5 miles of the Wasatch Fault, SOM’s structural engineering team utilized state-of-the-art, performance-based seismic design modeling/standards to ensure optimum response in the event of a major seismic event.
According to Peter Lee, Associate Principal with SOM, a linear and non-linear analysis was done on the maximum considered earthquake—7.5 magnitude. It was based on 21 different earthquake models, with the final model taking more than a month to compute.
“We’re looking at it on worst-case scenarios using the most advanced methods of our time to model and design it,” said Lee. “The building became much better in terms of performance and efficiency than a building designed to [standard] code. It’s a different challenge with a slender site.”
The tower’s superstructure is highlighted with reinforced concrete core walls, which have a lateral seismic-force-resisting system that consists of special ductile reinforced concrete core shear walls. Combined with the coupling beam construction extending from a pile and pile cap-supported deep foundation system to the penthouse roof at Level 26, there is a lot of excellent structural engineering to appreciate.
The slender core wall depth running east-west is just over 33 feet, with core shear walls ranging from 24- to 30-inch thick with concrete compressive strengths of 8,000 psi. The shear wall core is interconnected with ductile reinforced coupling beams at doorway and corridor openings.
Lee said the foundation includes an 11-foot deep matte foundation that sits on 363 24-inch diameter auger cast-in-place displacement piles drilled 110 feet into the ground. Huge outrigger grade beams help with transverse direction support that engage the core with perimeter columns at the basement level.
“The reason the building is on a deeper pile foundation is so that it can support the loads,” said Lee. “It’s a very reliable structural system for Salt Lake.”
“We had to tie the building down and include tension and compression piles,” said Tuite. “Because we have a thin building, we had to oversize the piles by three times. This is one of the most leading-edge seismic-resistant buildings in the world. In a seismic event, the top catwalk is designed to move over six feet and reset. There is more steel in the ground than in the building. Piles and pile caps have almost 50% more tonnage than the building.”
Tuite added that the introduction of the meetinghouse element required a higher code compliance level.
“It’s kind of ironic that if you have a public assembly space of over 300 [people], it actually pushes [the building] to a higher code criteria than having 3,000 office workers,” said Tuite.
The building includes 5,700 tons of steel, which includes a 1,900-ton hat roof truss system. On level five, the cantilever levels hang over an adjacent structure, rising 19 floors to the top of the building. The hat truss system carries the weight of the entire structure and cantilevers over the building’s four sides.
High Performance Glass/Curtain Wall System
The smoky-colored, all-glass curtain wall system is not only aesthetically pleasing but structurally resilient.
Exterior curtain wall systems had several interesting components, including a four-ply curved, laminated glass system that spans from the lobby floor to the underside of level three. Panels are 10 feet by 28 feet with no perpendicular mullions—a stark contrast to 111 Main, which also has an equally high glass lobby but is backed by vertical glass mullions.
“On this building, we were able to take advantage of the curved wall system and have the structural glass support itself,” said Lee. He said SOM collaborated with some of the best firms in the glazing and curtain wall, including Salt Lake-based subcontractor/installer Steel Encounters and structural façade engineers Eckersley O’Callaghan of New York City.
Tuite said the glass curtain wall system was designed to incorporate maximum deflection without any loss of glass.
“As a long-hold owner, we do things like that,” said Tuite. “This building theoretically can deflect five to six feet and not lose any glass.”
Installation required a yeoman-like effort from crews from Steel Encounters, said Project Manager Chad Johnson, a 27-year veteran of the industry.
“It’s just a huge accomplishment for the whole team,” said Johnson. “The uniqueness of the tower itself, with it being rounded corners all the way up makes it an amazing building. We had a lot of challenges, mainly just racing time. We dealt with Covid and still maintained our schedule. The field team did a phenomenal job dealing with what was in front of them. They were on the front lines, just trying to maintain the schedule. We had no time off and had to adjust on the fly with new protocols and procedures.”
The sheer size of the individual glass panels also was a major challenge for the firm. Johnson said the fact that the panels had vertical fin support was unique, and the first time has team has performed it in Utah. Each piece ranged from 4,000 lbs. to 7,800 lbs. with the heaviest pieces being the rounded corner panels on the lobby level. A special glass suction cup system designed by German-based Heavydrive included more than 100 cups to lift each panel via a hydro-crane. Johnson said his firm learned from its experience on 111 Main that a tower crane has too much bounce in the cable.
“The building has some of the largest freestanding glass panels that we’ve used on any project in the world,” added Duncan. “The detail is very impressive.”
Lobby Highlighted by Italian White Marble
One of the core design elements is the sleek white marble, supplied by Italian supplier and manufacturer Campolonhi from its Carrara quarry. Because of the pandemic, much of the stone selection occurred via video conferencing. Once the material was selected, a small team traveled to Italy to procure the stone. The design team used high-resolution photos to map the stone on 3D renderings with 2D elevations, creating a “virtual dry lay” of the walls and a set of rules of placement to guide the supplier.
The final installation result had an unparalleled level of craftsmanship that belies the almost entirely virtual process.
Jueschke said six large marble blocks were used with a tremendous final yield. Crews from Salt Lake-based Kepco+ had to perform almost perfectly, with the final result a testament to the firm’s skill and expertise. Kepco+ achieved 1/32 of an inch or better tolerances, a remarkable feat of precision.
“There was no replacement piece if a piece was cut wrong or broken,” said Jueschke. “We had a whole set of protections in place with the handling and the installation, to the point that we were babying the stone. We got a big win with Kepco’s work.”
The lobby also features a long, integral video screen that acts as an art piece, something that is dynamic and ever-changing. Duncan said “it extends the character of the lobby and makes the space a lot more active. Its movements work well with the curvature of the stone.”
The curved glass curtain wall system is one of the most distinctive, visual elements of the new high-rise and sets it apart from other buildings in downtown Salt Lake (photos courtesy SOM © Dave Burk)
Overall Teamwork Key to Successful Project
Compliments among the key players were effusive. Lewis praised Tuite for his expertise and ability to navigate tricky situations.
“Sean is one of the smartest people I’ve ever met,” he said. “He understands construction, understands motivation, finance, and quality. I learned early on that taking his cues was beneficial. If he thought something was an issue, every time he was right. At the end of the job, I felt like we had a great relationship with Sean and CCRI.”
Jueschke also praised the design team for its efforts to design a building with a high level of constructability. The prior relationships developed on 111 Main made it seem like an extension of that project.
“It was extremely beneficial having those relationships,” he said. “SOM is a fantastic architect and engineer. Having that behind us was beneficial to hitting the ground running and continuing those relationships. It’s no secret that there is a ‘grinding of gears’ between entities on a project of this magnitude, but we had those prior relationships to fall back on. Knowing what their design intent is was important—it’s not something you can communicate through documents. We all had expectations.”
Sobel added, “It was a very collaborative process with the client and Okland, and that made for a great project. The best projects are the ones that everyone enjoys. In the end, everyone is super excited that we delivered what we hand in our mind’s eye from the beginning.”
95 State at City Creek
Owner: City Creek Reserve, Inc.
Owner’s Rep: Sean Tuite
Developer: City Creek Reserve, Inc.
Size
Site Area: 32,085 SF
Project Area: 585,900 SF
Building Height: 395 ft.
Stories: 25
Design Team/Consultants
Architect: Skidmore, Owings & Merrill
Civil Engineer: Great Basin Engineering
Electrical Engineer: Syska Hennessy Group
Mechanical Engineer: Syska Hennessy Group
Structural Engineer: Skidmore, Ownings & Merrill
Geotechnical Engineer: Consolidated Engineering Laboratories
Landscape Design: MGB+A
Parking: International Parking Design
Fire Protection: Jensen Hughes
Lighting Design: Luma
Door Hardware: Allegion
Vertical Transportation: EWCG
Wind: RWDI
Acoustics/AV/Security: Shen Milson & Wilke
MEP/Sustainability/Energy Modeling: Syska Hennessy Group
LEED/WELL Consultants: Zinner Consultants
Construction Team
General Contractor: Okland Construction
Concrete: Okland Construction
Concrete Reinforcement: Harris Rebar
Plumbing: Archer Mechanical
HVAC: Archer Mechanical; B2Air
Electrical: Hunt Electric
Masonry: IMS Masonry, Kepco+, RJ Masonry
Drywall/Acoustics: CSI Drywall, Inc.
Painting: Grow Painting
Tile/Stone: IMS Masonry; Kepco+; RJ Masonry, Metro
Carpentry: Boswell Wasatch
Flooring: Spectra, Kepco+
Roofing: Utah Tile & Roofing
Glass/Curtain Wall: Steel Encounters, Inc.
Waterproofing: Waterproofing West
Steel Fabrication & Erection: SME Steel
Excavation & Demolition: Jones Excavating
Landscaping: Intermountain Plantings
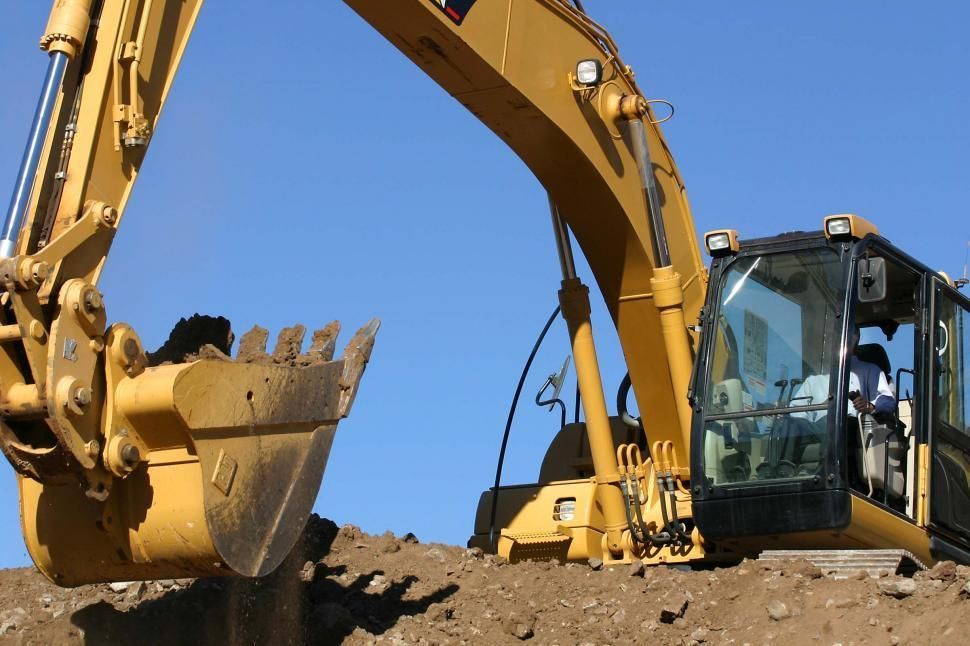
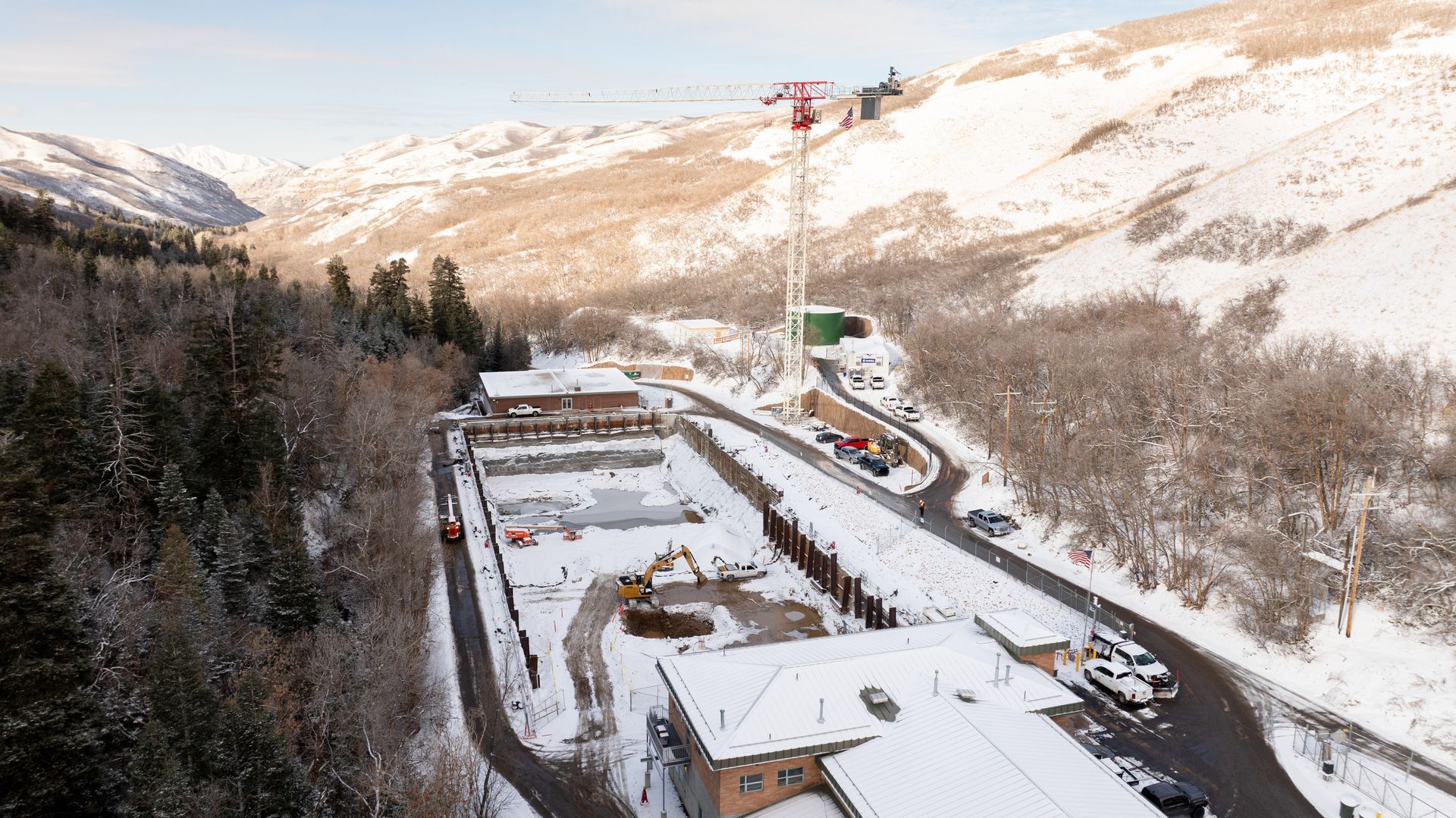
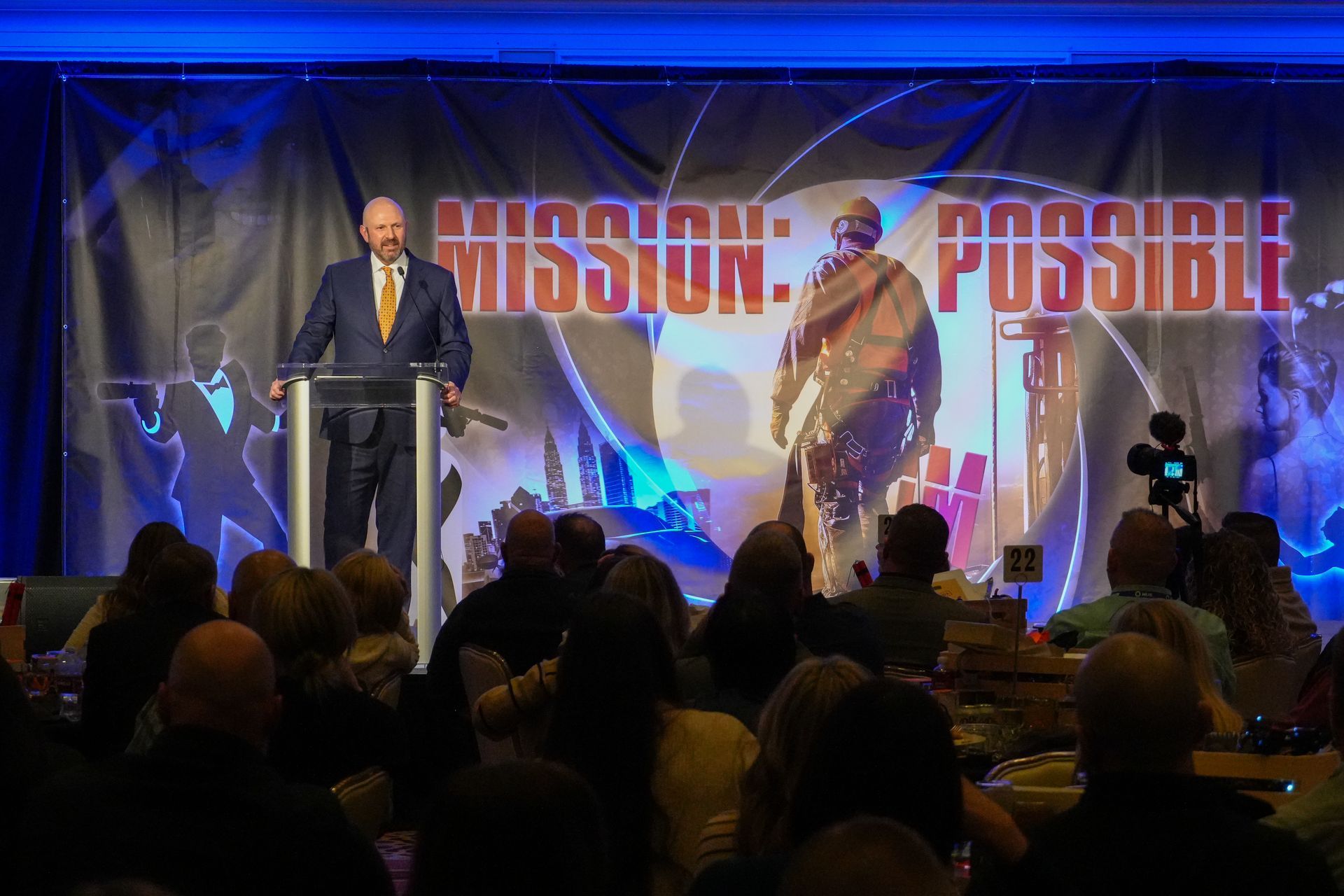
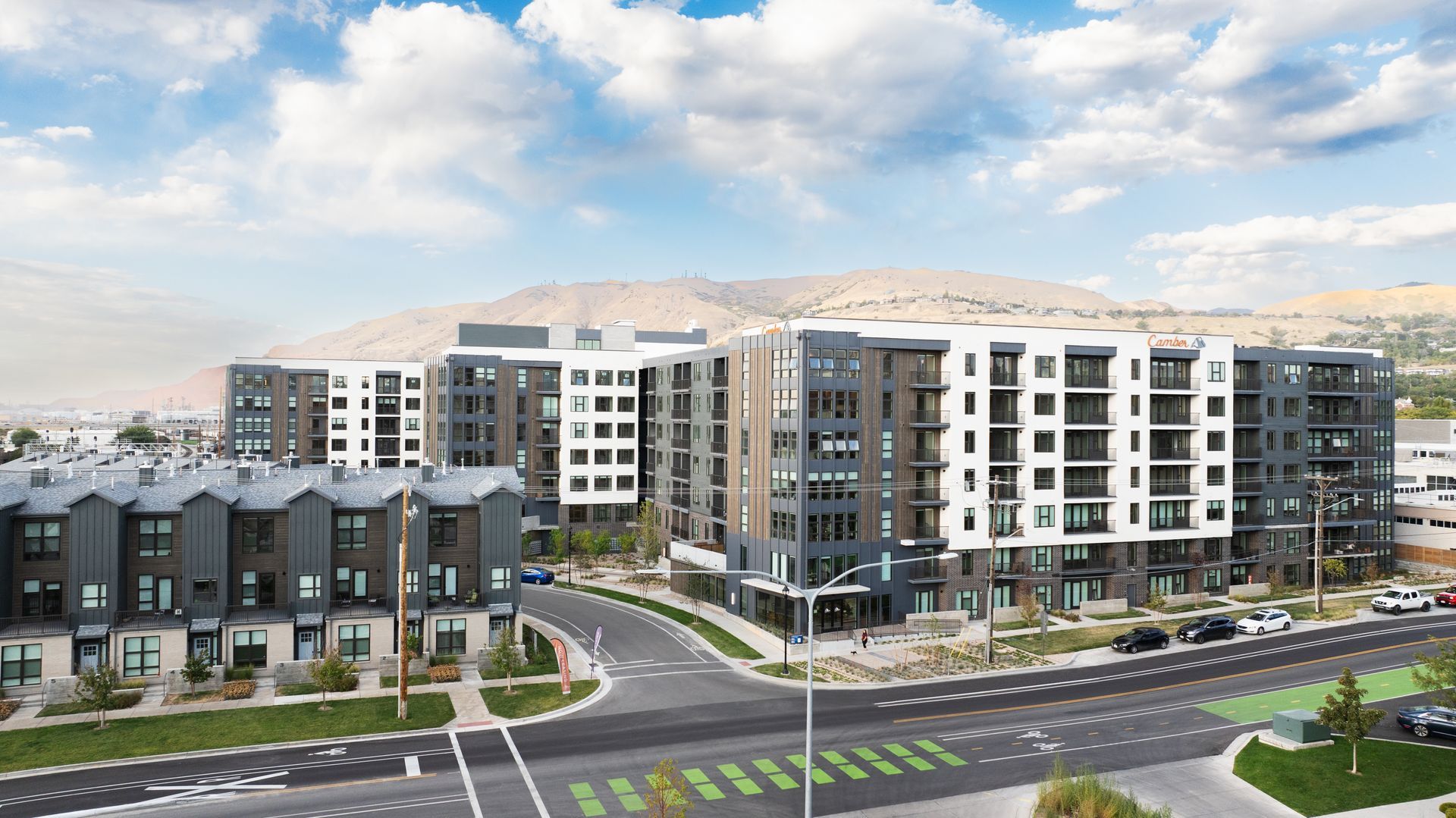
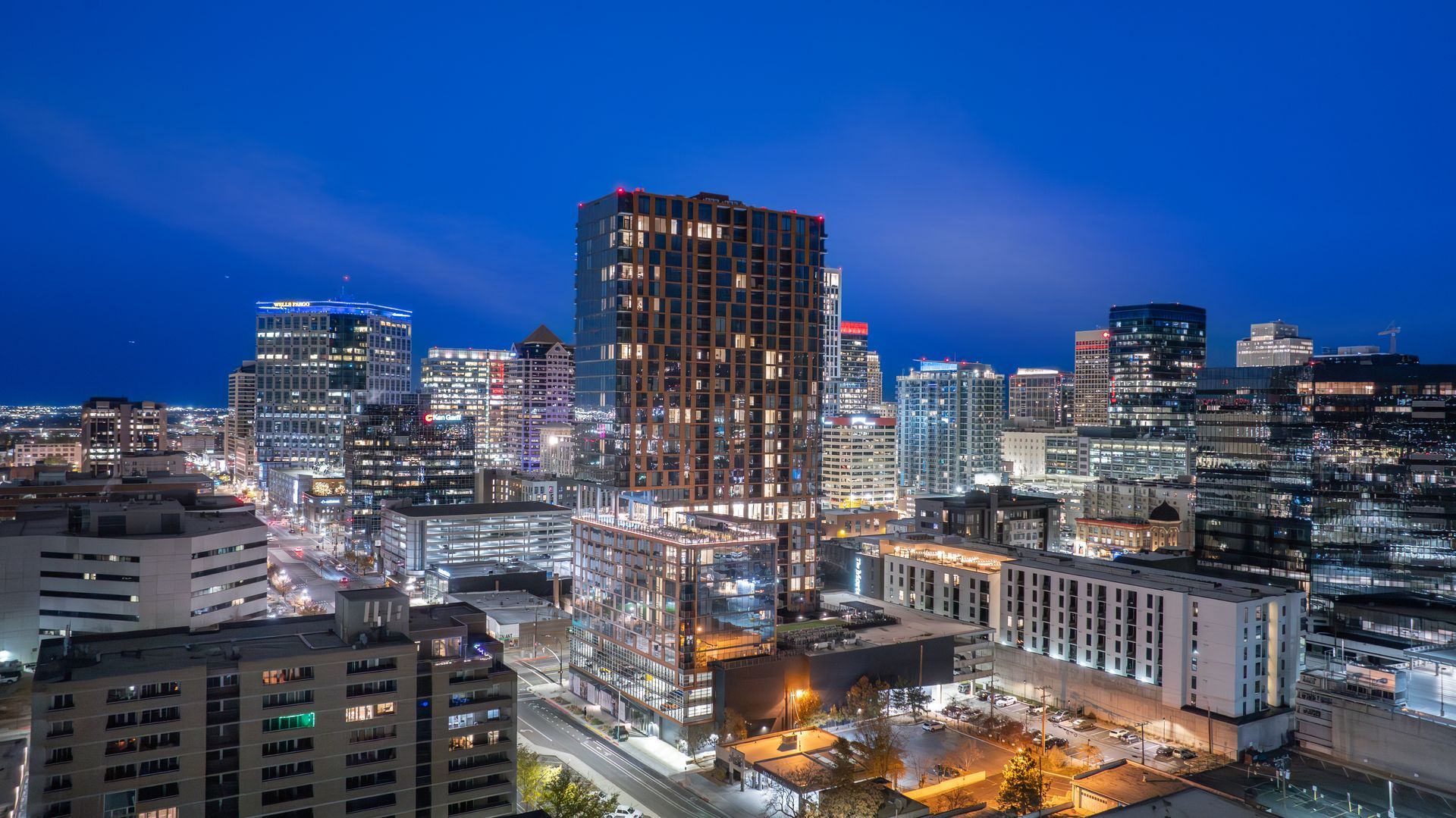
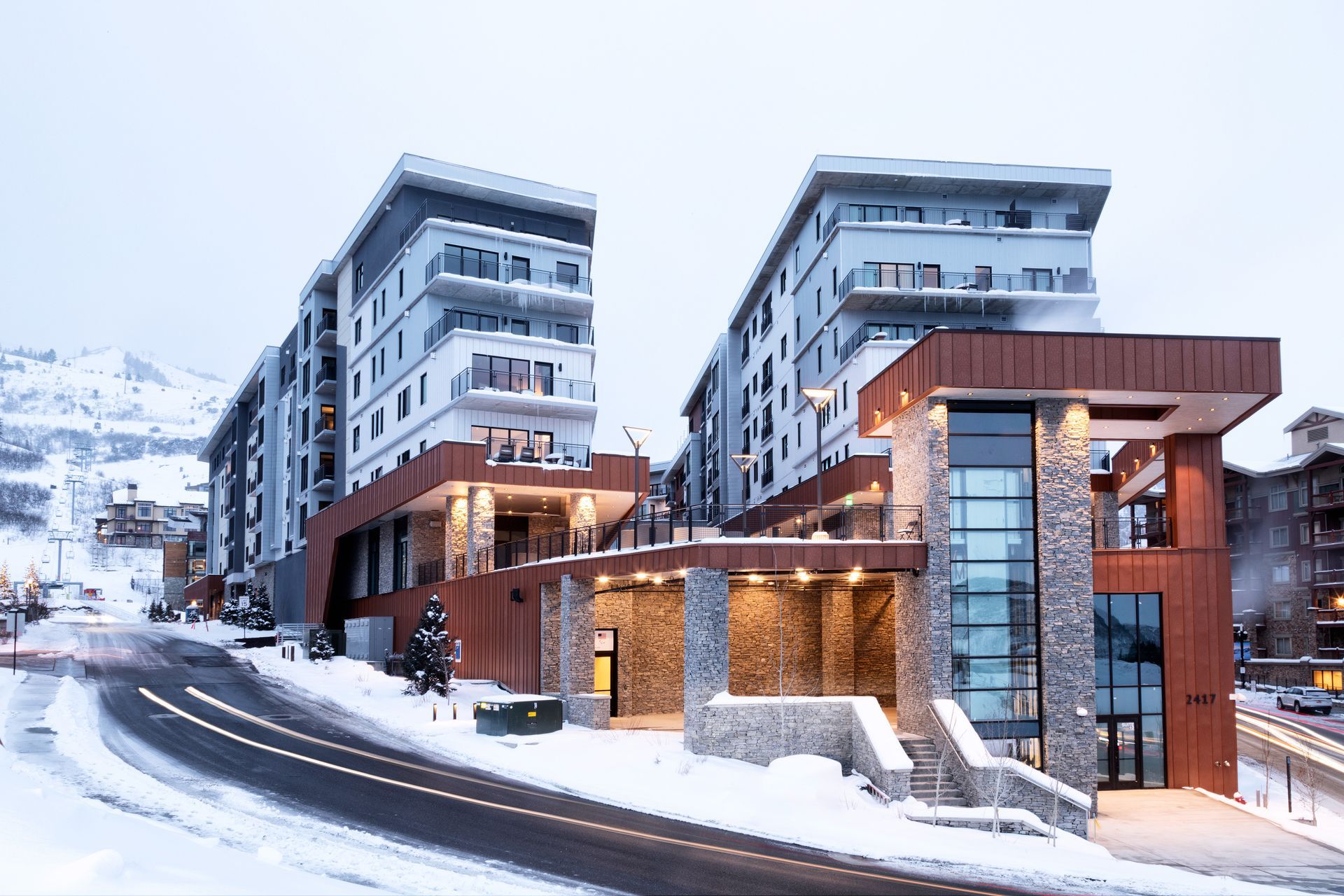
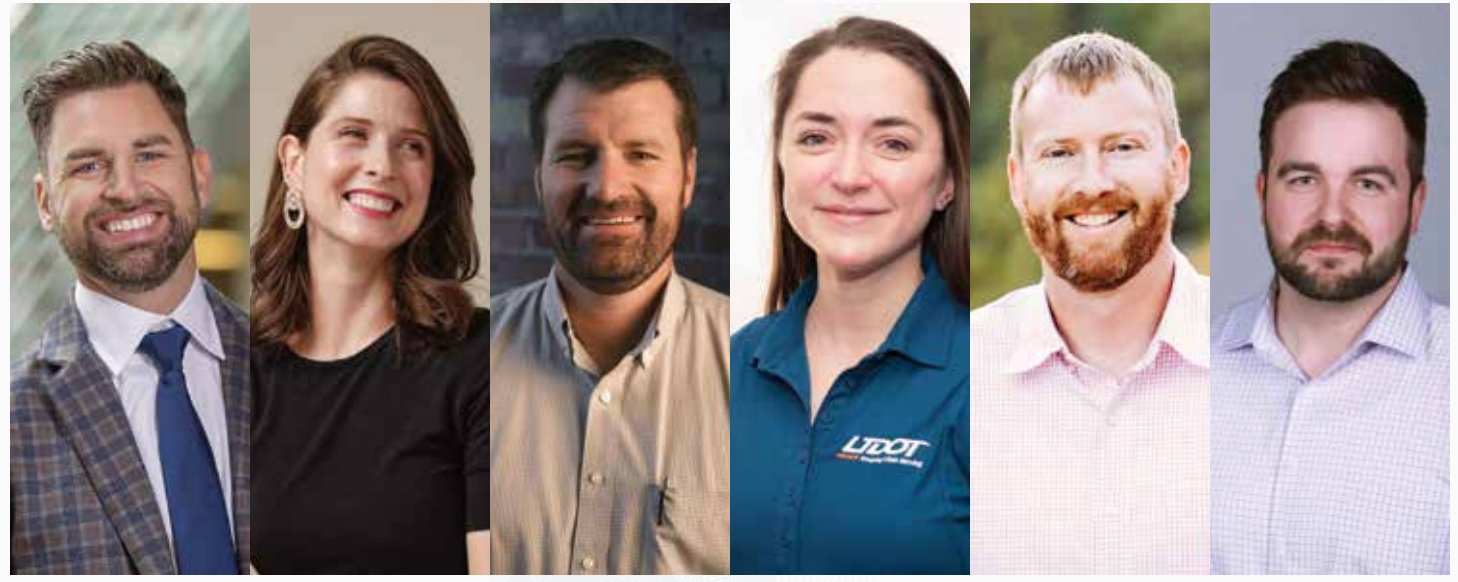
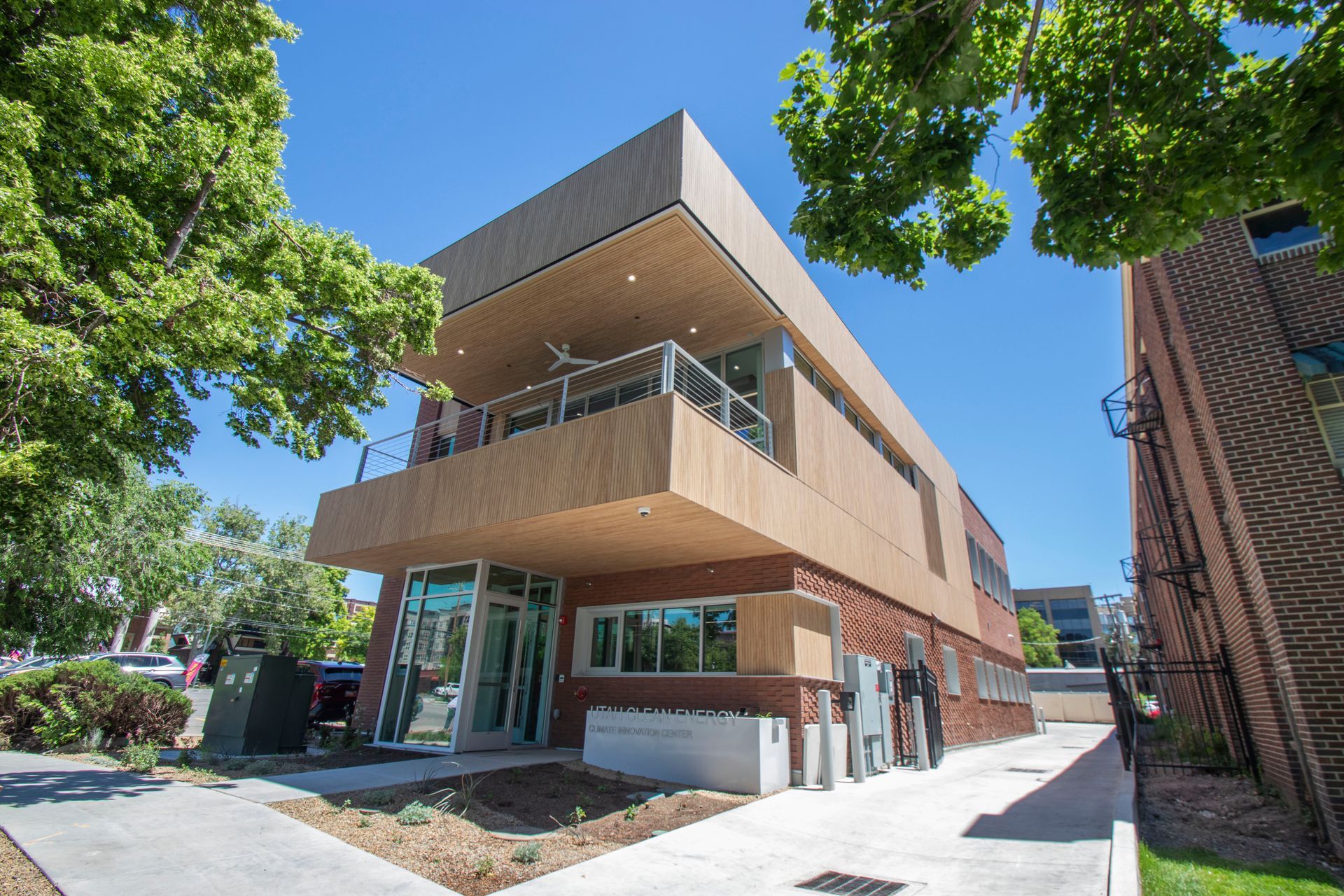